Die Geschichte der Pulverbewertung - Teil 2
Im letzten Bericht haben wir die Bewertung von Metallpulvern erörtert. In der pulvermetallurgischen Industrie ist der Prozess des Knetens (Vermischen des Hauptrohstoffs mit den Nebenstoffen) unvermeidlich. Dieses Mal werden wir uns mit der Knetphase befassen.
Die Kunst der Materialmischung
Metallpulver und Harzpulver werden geknetet, um das Ausgangsmaterial in Form von Pellets für das Spritzgießen herzustellen. Die Menge des Harzes ist ein wichtiger Faktor, um nicht nur die Fließfähigkeit des Spritzgussverfahrens, sondern auch die Maßgenauigkeit des fertigen Bauteils zu steuern. Die optimale Harzmenge für Metallpulver verschiedener Partikelgrößen darf weder zu viel noch zu wenig sein, und die Methode zur Bestimmung der Harzmenge, die Methode zum Kneten und die Bewertung des Mischungsgrads sind ein Gebiet mit hohem Know-how.
Tatsächlicher Harzgehalt
Im Idealfall ist jedes Metallpulver mit einer dünnen Schicht Harz bedeckt, das homogen und unabhängig verteilt ist. Daher ist die Oberfläche des Metallpulvers wichtig für die Bestimmung der optimalen Harzmenge. Die Gasadsorptionsmessung nach der BET-Theorie ist die Standardmethode zur Berechnung der Oberfläche pro Masseneinheit des Pulvers, aber wie bereits im vorherigen Bericht erwähnt, möchten wir hier die schwierige Theorie beiseite lassen und eine weitere Vor-Ort-Methode einführen, wir werden über die analoge Messmethode sprechen, die Leinsamenöl-Adsorptionsmethode. Bei dieser Methode können Sie die Oberfläche des Pulvers mit Ihren eigenen Augen und Händen fühlen. Die Öladsorption ist eine Methode zur Bewertung der Oberflächeneigenschaften von Pigmenten oder Pulvern, die in JIS K5101-13-1:2004 (ISO 787-5:1980) beschrieben ist. Einige Tropfen Öl werden dem Pulver zugegeben und mit einem Spatel homogen vermischt. Der Endpunkt ist erreicht, wenn das Pulver zu einem vollständigen, matschigen Klumpen wird.
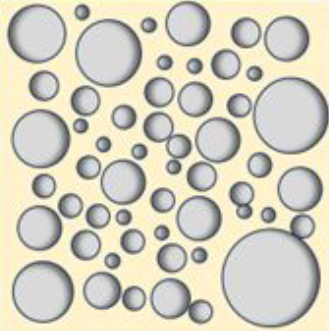
Die Fotos unten zeigen die Veränderung des Aussehens während des Öladsorptionstests mit Edelstahlpulver. Ausgehend von (1) wird nach und nach ein Tropfen Öl hinzugefügt, und aus dem trockenen Zustand beginnt sich nach und nach ein kleiner Klumpen zu bilden, der sich dem Endpunkt bei (4) nähert. Dann, mit dem nächsten Tropfen von (4) nach (5), kommt es zu einer dramatischen Veränderung, und es wird zu einem kompletten matschigen Klumpen. Das ist großartig! In diesem Moment kann man fühlen, dass die gesamte Oberfläche des Pulvers mit Öl benetzt wurde, was viel befriedigender ist, als nur die Zahlen auf dem Bildschirm zu betrachten. Das rechte Diagramm zeigt die Beziehung zwischen dem durchschnittlichen Partikeldurchmesser und der Öladsorption von 5 verschiedenen Edelstahlpulvern, die wir in der Serienproduktion verwenden. Die Öladsorption nimmt mit zunehmendem Partikeldurchmesser ab, aber es sind auch signifikante Unterschiede in der Zusammensetzung der verschiedenen Edelstahlserien zu erkennen. Dieser intuitive Test gibt uns einen Anhaltspunkt für die optimale Menge an Harz, die für die MIM-Herstellung nützlich ist.
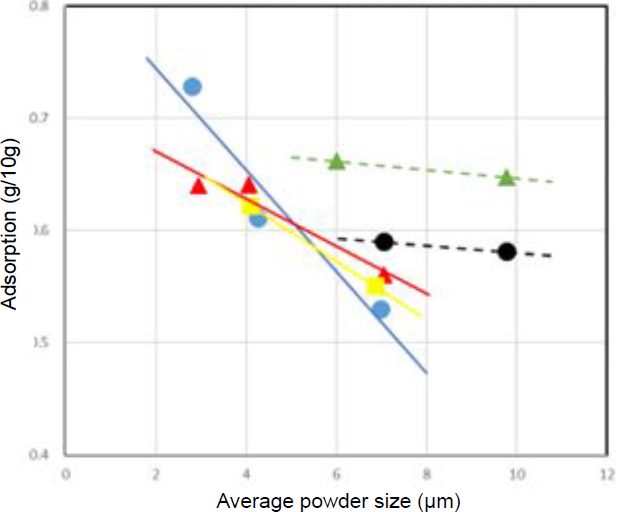

Sobald die Mischungsmengen von Metallpulver und Harz bestimmt sind, werden sie geknetet und zu Pellets verarbeitet. In der nächsten Ausgabe werden wir darüber sprechen, wie der Grad der Knetung zu bewerten ist.
Download der PDF-Datei
Fazit
Risse, Absacken oder Blasenbildung werden häufig als Folge des Aufquellens des Bindemittels und/oder der unterschiedlichen Eigenspannungen zwischen der Oberfläche und dem Inneren beobachtet. Diese Probleme lassen sich durch die Auswahl geeigneter organischer Lösungsmittel und durch Temperaturkontrolle vermeiden.
Das katalytische Entbindern nutzt die Sublimation des Bindemittels, wodurch es möglich ist, das Bindemittel in relativ kurzer Zeit zu zersetzen und die Verformung zu minimieren. Bei einer stark sauren Atmosphäre ist die Auswahl an Metallwerkstoffen jedoch begrenzt.
Beim Sinterprozess setzt die Halsbildung („Necking“), d. h. die Ausbildung von Brückenbindungen zwischen Metallpulverkörnern durch thermische Diffusion, bei Erreichen der Sintertemperatur ein. Sobald dieses Necking einsetzt, wird eine Schrumpfung beobachtet, die die Dichte erhöht. Bevor das Necking einsetzt, sollten daher alle organischen Bestandteile zersetzt und das Gas zwischen den Pulverkörnern entfernt werden. Im Sinterprozess führen unerwünschte chemische Reaktionen wie Oxidation oder Karbonisierung zum Verlust mechanischer Eigenschaften, weshalb zu Beginn des Prozesses eine präzise Atmosphärensteuerung mit niedriger Heizrate erforderlich ist. Wenn die Sintertemperatur erreicht ist, können außerdem einige pflanzenbasierte Bindemittel verdampfen.