Was ist μ-MIM®?
Die 4 besten Argumente für die Fertigung hochpräziser Bauteile mit μ-MIM®
Hohe Toleranz
Mit über 25 Jahren Forschung und Entwicklung in der MIM-Fertigungstechnologie haben wir eine beispiellose Toleranzzufriedenheit im gesinterten Zustand erreicht. Bei herkömmlichem MIM liegt die engste Toleranz bei ± 30 μm, während μ-MIM® ± 10 μm erreicht.
Verglichen mit der neuesten Bearbeitungstechnologie sind die erreichten Toleranzen zwar geringer, aber immer noch wettbewerbsfähig mit der konventionellen Bearbeitung. Darüber hinaus handelt es sich bei der μ-MIM®-Technologie um eine Endkontur-Fertigungstechnologie, bei der nur eine minimale Nachbearbeitung erforderlich ist, um das Risiko von Toleranzabweichungen in 3D-Lagen zu verringern. Produktivität und Präzision sind die einzigartigen Stärken der μ-MIM®-Technologie, die Ihnen hilft, Ihr ideales Metallteil zu realisieren und auf den Markt zu bringen.
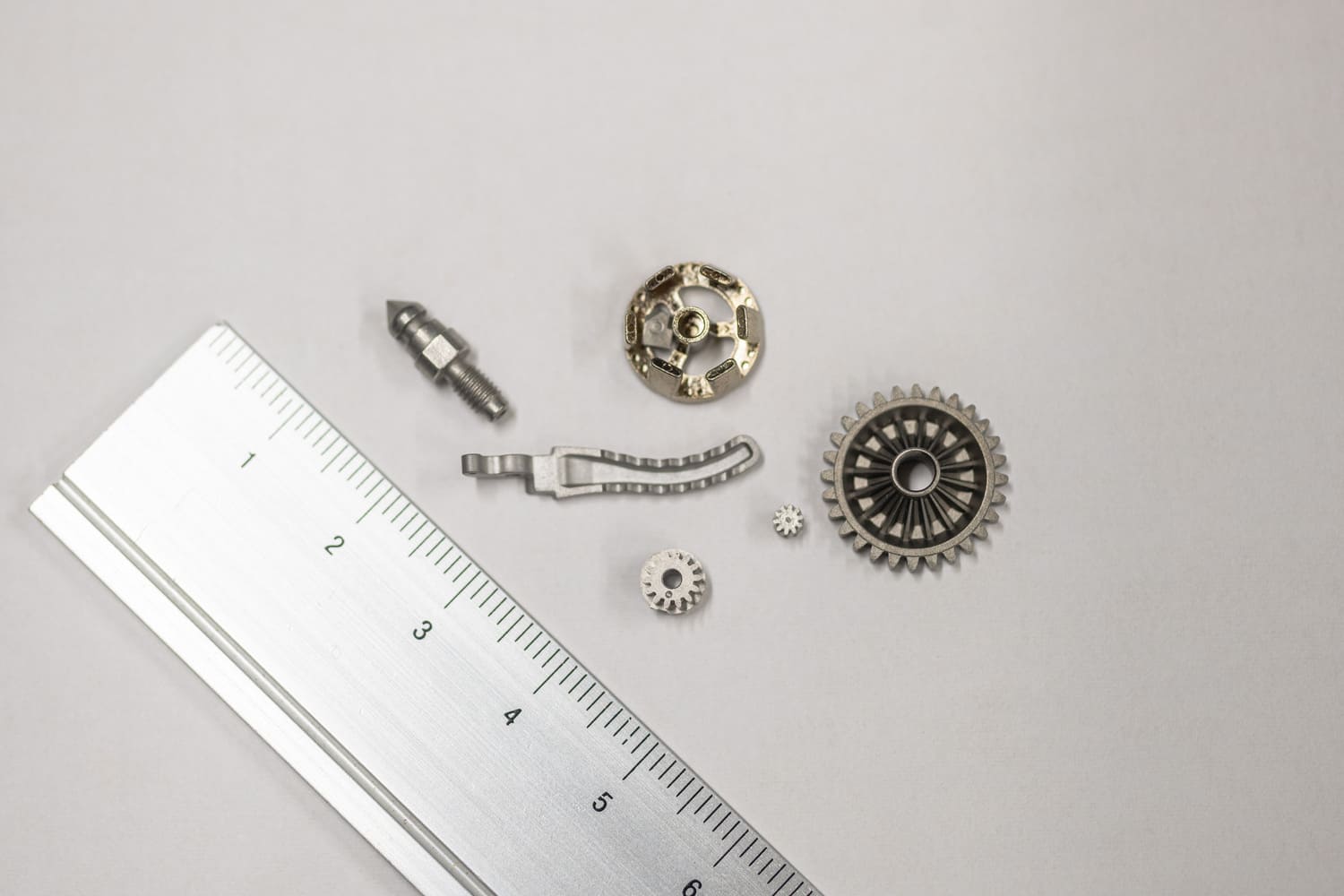
Werkstoffvielfalt
Dies ist auf unsere ursprüngliche Rohstoffverarbeitung zurückzuführen, die wir auf der Grundlage unseres Wissens und unserer Erfahrung in der Geschichte des Kunststoffspritzgusses entwickelt haben. Wir stellen das Bindemittel selbst her.
Da unsere Vorlaufzeit für die Entwicklung des Ausgangsmaterials relativ kurz sein könnte, kann auch neu entwickeltes Legierungspulver für die Produktion verwendet werden, sofern die richtige Größe und Form des Pulvers für die Beschaffung verfügbar ist.
Wir sind in der Lage, das Ausgangsmaterial für die stabile Produktion jedes Produkts zu optimieren, und neu entwickeltes Legierungspulver kann auch für die Produktion verwendet werden.
Bitte kontaktieren Sie uns, auch wenn das Material nicht in der Liste enthalten ist.
Designfreiheit
Die μ-MIM® Technologie wurde mit dem Fokus auf die Serienfertigung kleiner komplexer Designs entwickelt, so dass die Produktion mit minimalem Nachbearbeitungsaufwand realisiert werden kann.
Da die μMIM®-Technologie mit Schwerpunkt auf der Serienfertigung kleiner komplexer Designs entwickelt wurde, sind wir in der Lage, kleine Strukturen oder unmöglich zu entformende Designs mit einem Minimum an zusätzlicher Bearbeitung herzustellen.
Darüber hinaus lässt sich mit unserer 3D-μMIM®-Technologie ein so hohes Maß an Designfreiheit erreichen, wie Sie es von herkömmlichem MIM nicht erwarten können.
Mit unserer μ-MIM®- und 3D-μMIM®-Technologie können Sie Ihre schwer zu bearbeitenden Designs in Serie produzieren.
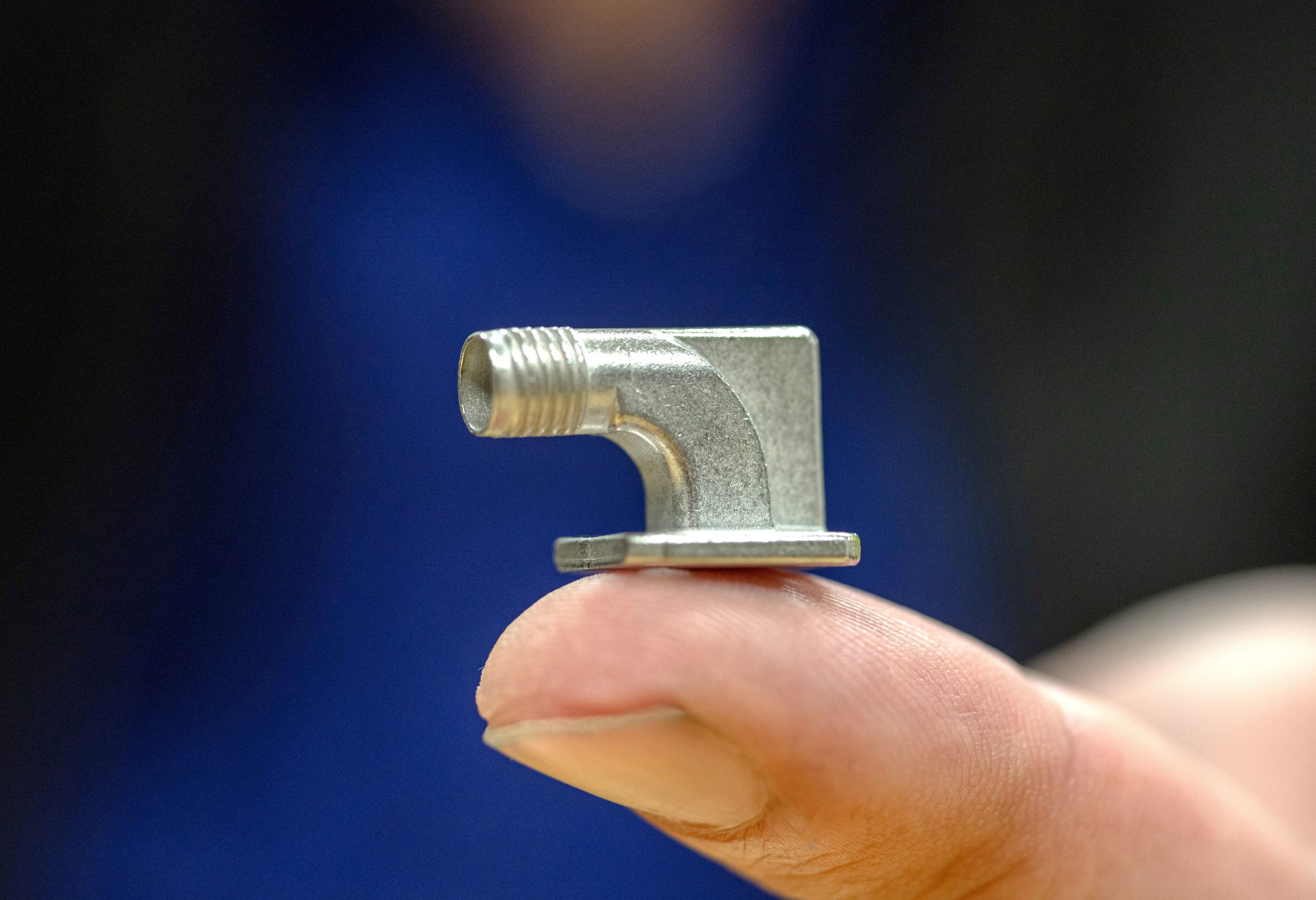
Stabile Massenproduktion
Wir wissen, dass die Herstellung kleiner, komplexer Metallteile eine noch bessere Prozesskontrolle erfordert als das herkömmliche MIM, da die Qualität des vorangehenden Schritts einen noch größeren Einfluss auf die Parameter des nachfolgenden Schritts hat.
Die Herstellung kleiner, komplexer Metallteile erfordert eine gute Gleichmäßigkeit des Ausgangsmaterials, da die Produktgröße kleiner als die Pelletgröße sein kann.
Wir haben unseren Produktionsprozess vom Ausgangsmaterial bis zum Sintern sowie den abschließenden Messprozess im Rahmen des zertifizierten Qualitätssicherungssystems ISO 13485 genau kontrolliert.
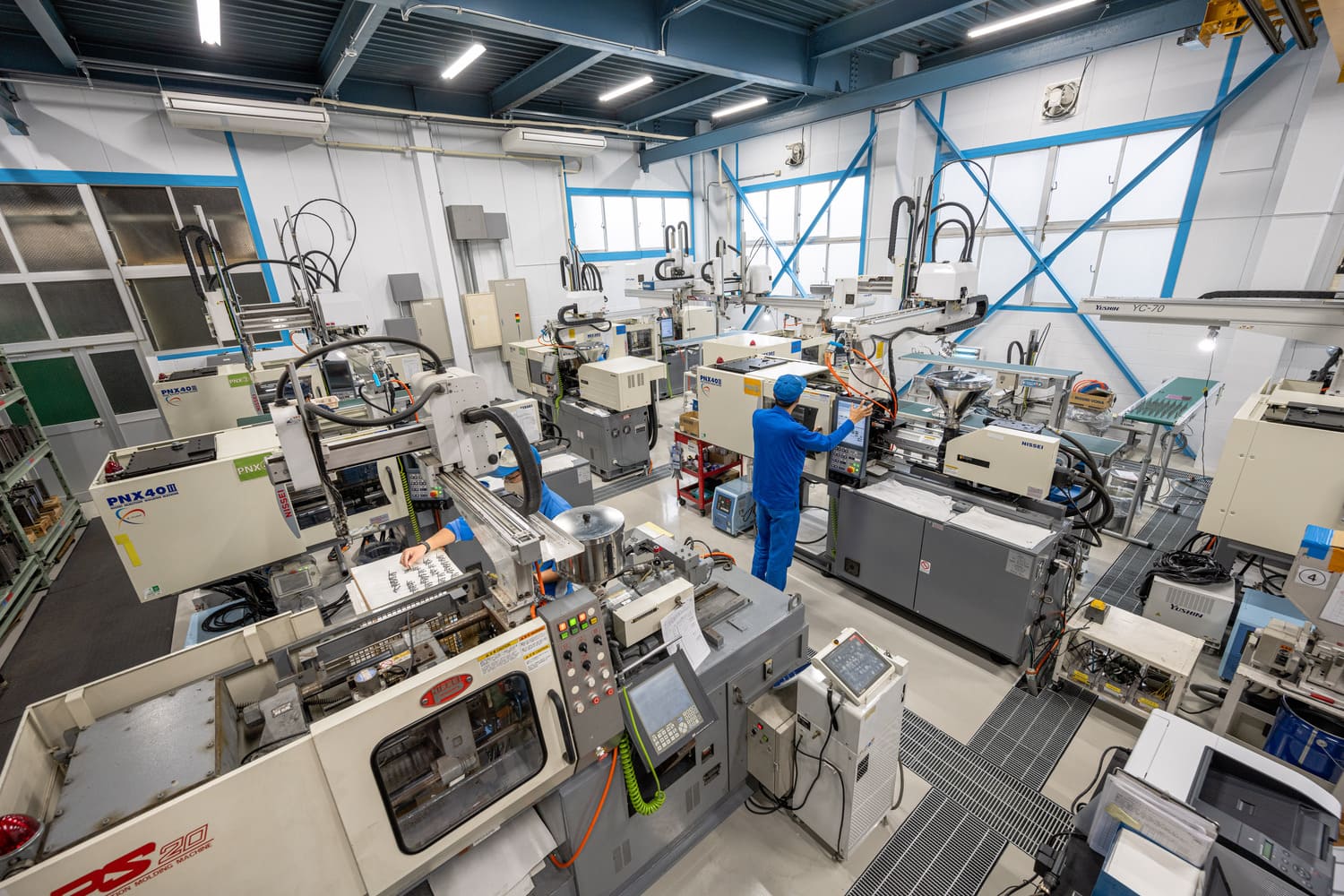
Was wir unseren Kunden bieten können
Herausragende Kompetenz
Breitestes Spektrum an Werkstoffen
Winzige Komponenten
Designfreiheit
Stabile Serienproduktion
Hohe Qualität
Teile kleiner als ein Reiskorn
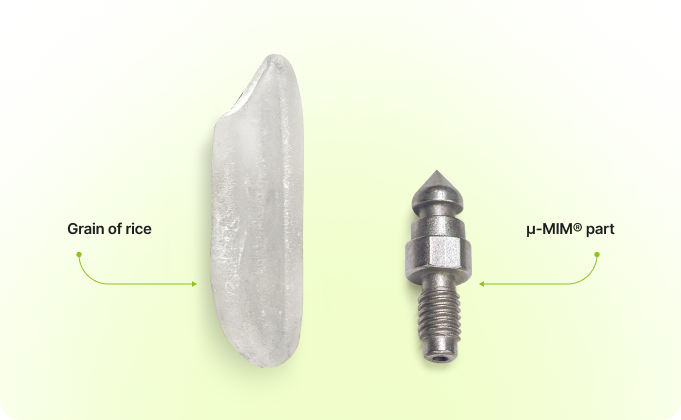
Hohe Genauigkeit, Dichte, Festigkeit und Oberflächengüte
Hohe Genauigkeit
Hohe Dichte
Hohe Festigkeit
Hohe Oberflächengüte
Werkstoffe
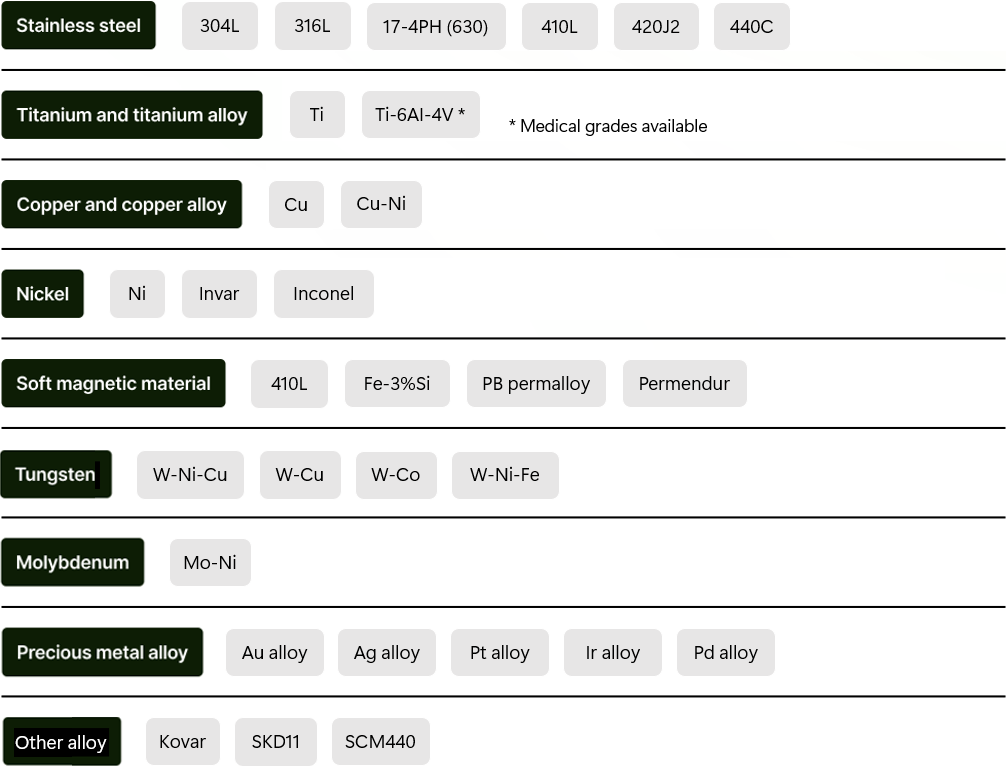
3D-μMIM®-Technologie
3D-µMIM® ist unser einzigartiges Lost-Core-Verfahren, das die Massenproduktion von Bauteilen mit komplexen Geometrien mit Hohlstrukturen und Hinterschneidungen ermöglicht, die mit konventionellem MIM oder spanender Bearbeitung nur schwer herzustellen sind.
Zunächst wird eine Kunststoff-Opferform (SP-Form) in einer Form hergestellt und in eine andere Form eingelegt; die SP-Form wird während des Entbinderns und Sinterns vollständig demontiert, und am Ende wird ein 100%iges Metallbauteil hergestellt.
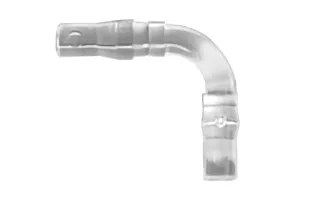
Kunststoff-Opferform
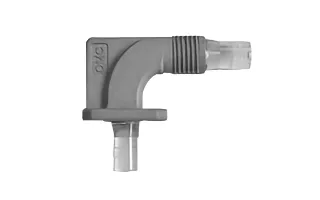
Einspritzung von metallischem Feedstock
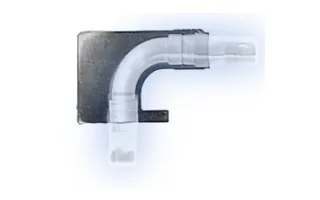
Entfettung und Sinterung
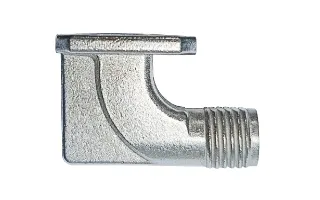
Gesintertes Bauteil
Freiform-Bauteilbeispiele mit 3D-μMIM®
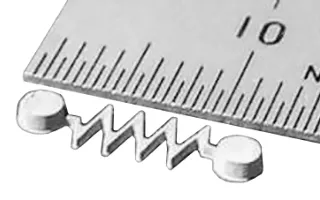
Wellenfeder
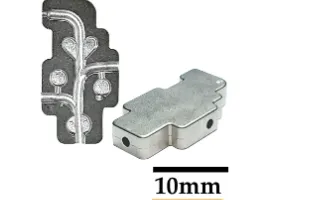
Innenliegende gekrümmte Fließkanäle
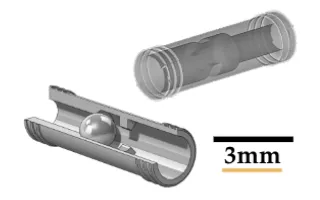
Hohle Struktur
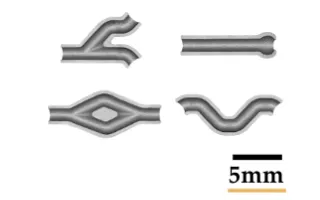
Mikrorohr
LMM 3D-Druck X μ-MIM®-Technologie
µ-MIM® Auswerte- und Messtechnik und Qualitätssicherung
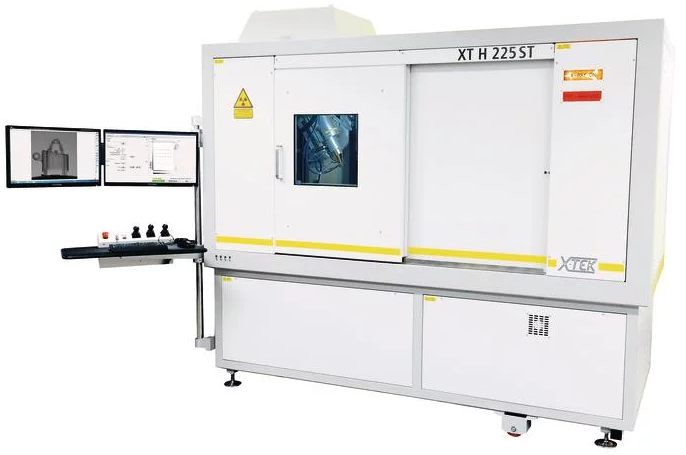
Röntgen-CT
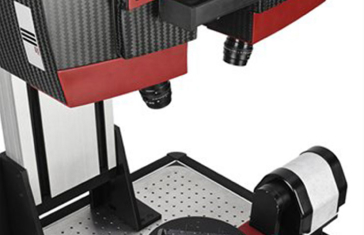
Optisches 3D-Messsystem
Unterschiede zwischen MIM und μ-MIM®
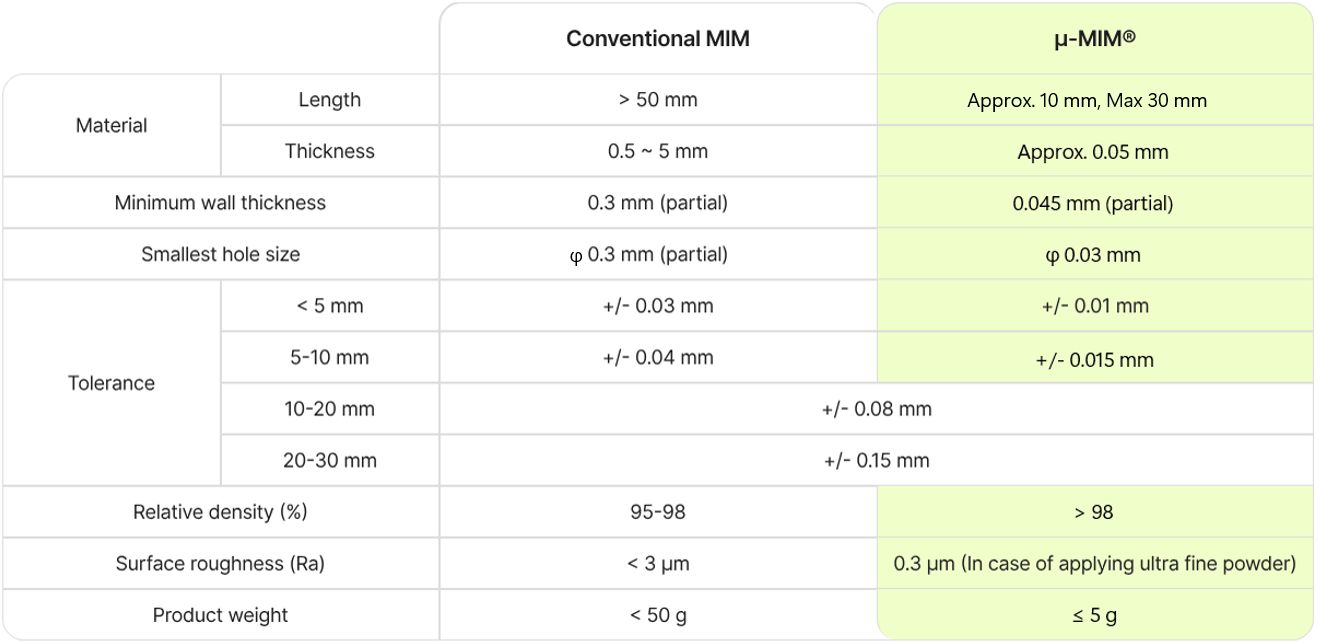
Vergleich mit anderen Fertigungsverfahren
Wie wir Ihnen helfen, Ihre technologischen Herausforderungen zu bewältigen
Fall 01
Die Herausforderung
Da die Form des Bauteils zu komplex war, um es in einem Arbeitsgang herzustellen, wurden mehrere Teile separat gefertigt, die anschließend zu einem einzigen Teil zusammengefügt werden mussten.
Die Lösung
Wir können Teile bereits in Endkontur fertigen, indem wir eine Matrize in einer integrierten Form verwenden. Das hilft, die Kosten zu senken und die Lieferzeit zu verkürzen, und führt auch zu einer Verkleinerung.
Fall 02
Die Herausforderung
Da das Material eine komplexe Form hatte und schwer zu verarbeiten war, weigerten sich andere Unternehmen, es herzustellen.
Die Lösung
Wir sind in der Lage, Bauteile mit komplexen Formen und schwer zu bearbeitenden Materialien zu fertigen, und können so einen wertvollen Beitrag zur Entwicklung völlig neuer Produkte leisten.
Fall 03
Die Herausforderung
Es entstanden Grate usw., eine Nachbearbeitung war erforderlich, und die Ausbeute war gering.
Die Lösung
Endkonturfertigung hat die Nachbearbeitung überflüssig gemacht und eine hochpräzise Produktion ermöglicht.
Fall 04
Die Herausforderung
Die maschinelle Bearbeitung stieß in der Massenproduktion an ihre Grenzen, so dass das Bauteil nicht in der gewünschten Menge hergestellt werden konnte.
Die Lösung
Wir bieten die Fertigung in Dimensionen an, die durch maschinelle Bearbeitung nicht erreicht werden können, sowohl in Bezug auf die Menge als auch auf die Form, was zu niedrigeren Kosten und kürzeren Lieferzeiten führt.
Warum andere Unternehmen gerne mit uns zusammenarbeiten
Laden Sie unseren Unternehmensflyer über unsere µ-MIM®-Technologie herunter
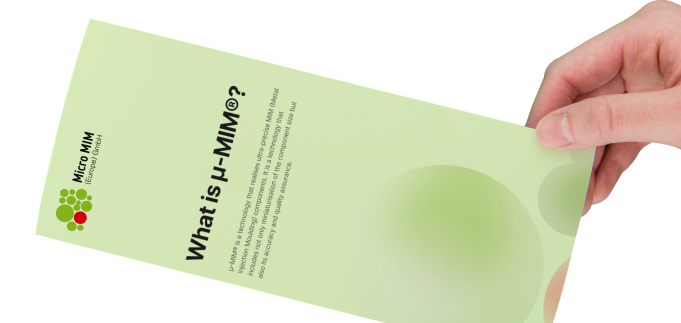
Vereinbaren Sie noch heute einen ersten Beratungstermin mit einem unserer Experten
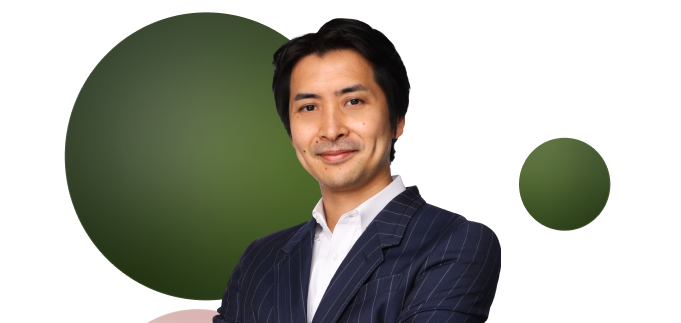