Gerät
LMM-3D-Drucker: Hammer Lab35
Das LMM-Verfahren (Lithography-based Metal Manufacturing) zeichnet sich durch die Formgebung durch Photopolymerisation einer Mischung aus lichtempfindlichem Harz und Metallpulver aus. Durch das Licht ist die Laminierung extrem stabil und kann hochpräzise und kleine Komponenten realisieren.
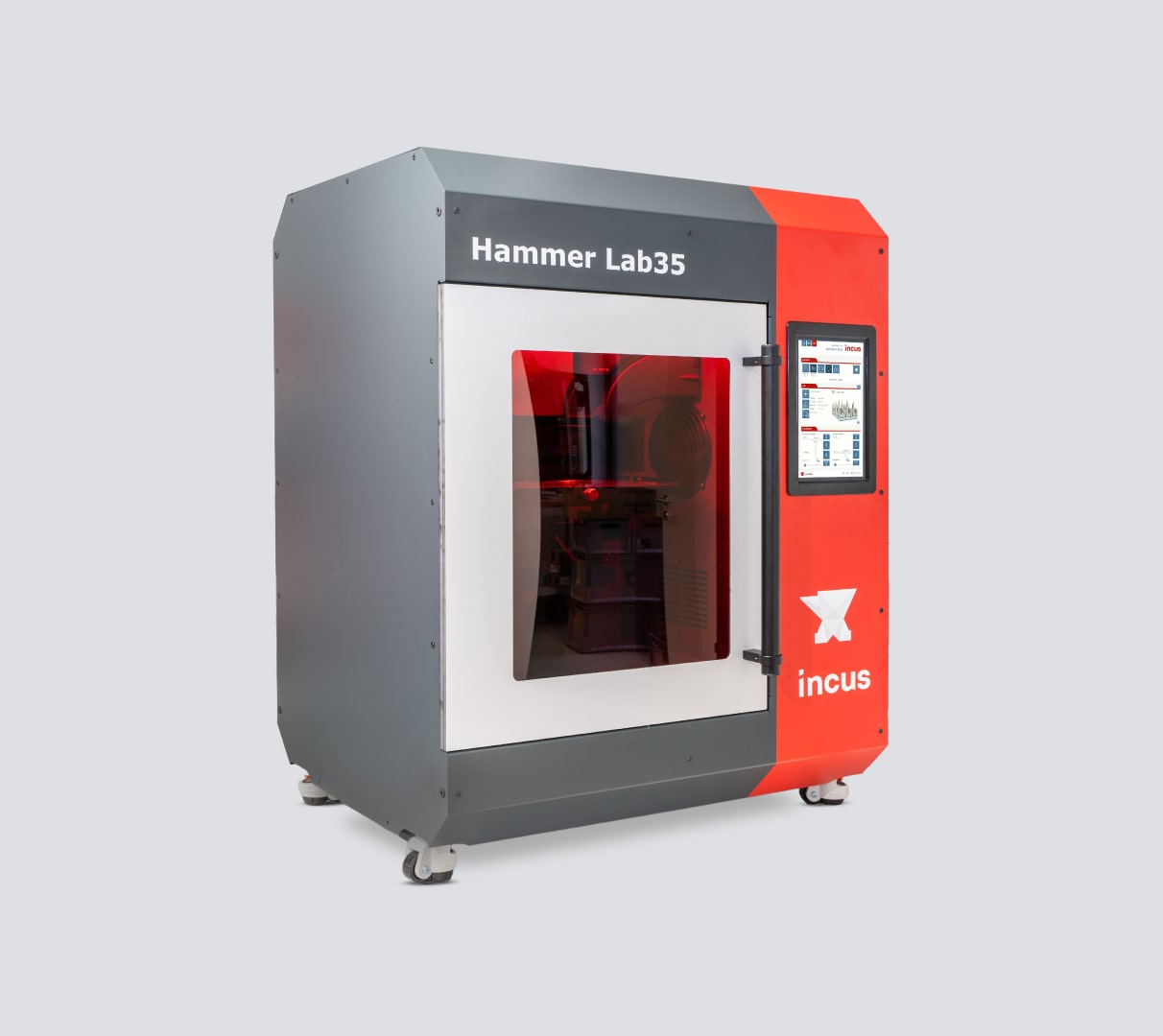
Maschinenparameter des Hammer Lab35
Hergestellt von
Incus GmbH
Laterale Auflösung
35 / 15 μm (angepasst)
Anzahl der Pixel (X, Y)
2560 x 1600
Bauvolumen (X, Y, Z)
89,6 x 56 x 120 mm
Schichtdicke
10 - 100 μm
Bauraum
Volle Klimakontrolle
Baugeschwindigkeit
Bis zu 250 Schichten/h
Druckgeschwindigkeit
Bis zu 100 cm³/h
3D-Druckverfahren
Bei der LMM-Methode des 3D-Drucks wird das folgende Verfahren für die Modellierung verwendet.
Zunächst werden CAM-Daten aus 3D-CAD-Daten erstellt, und der 3D-Drucker wird für die Modellierung verwendet. Danach wird das Werkstück mit Ausnahme des gehärteten Teils durch Fotopolymerisation geschmolzen, und anschließend wird ein Werkstück aus Metallpulver und lichtempfindlichem Harz hergestellt. In diesem Stadium ist das Metallpulver noch instabil, da die Dichte des Metallpulvers nicht hoch ist und ein zusätzliches Material, das Harz, vorhanden ist (dieser Zustand wird auch als Grünkörper bezeichnet).
Das erhaltene Werkstück wird im nächsten Prozess "entwachst und gesintert". In diesem Stadium wird das Harzmaterial geschmolzen und verflüchtigt (entfettet), und die verbleibenden Metallpulver werden agglomeriert und gesintert. Bei der LMM-Methode (und der Binder-Jet-Methode) ist dieser Sintervorgang ein wichtiger Prozess, der die Qualität des endgültigen Teils bestimmt, und Kenntnisse und Know-how in Bezug auf die Sinterung sind wichtig. Durch einen sorgfältig gesteuerten Entparaffinierungs- und Sinterungsprozess wird die Dichte des fertigen Metallteils auf 98 % oder mehr erhöht, und die Oberfläche wird so bearbeitet, dass eine Hochglanzpolitur möglich ist.
Zusammenfassend lässt sich sagen, dass bei der LMM-Methode Licht verwendet wird, um aus einem Gemisch aus lichtempfindlichem Harz und Metallpulver durch Fotopolymerisation einen Grünkörper zu formen, der nach dem Entparaffinierungs- und Sinterungsprozess die gleiche Metallmodellierung wie die MIM-Methode ergibt. Der Vorteil dieser Methode besteht darin, dass die Material- und Sintertechnologien von μ-MIM® direkt eingesetzt werden können, was für die Überprüfung nützlich ist. Da mit Licht gearbeitet wird, ist die Stapelung äußerst stabil und eine Teilegenauigkeit von ±0,2 % oder weniger ist möglich. Da das Werkstück nach der Formgebung ohne Kraftaufwand entnommen werden kann, ist es außerdem möglich, filigrane und komplexe Formen zu formen. Als Ergebnis kann eine mit μ-MIM® vergleichbare Qualität erreicht werden.
Zunächst werden CAM-Daten aus 3D-CAD-Daten erstellt, und der 3D-Drucker wird für die Modellierung verwendet. Danach wird das Werkstück mit Ausnahme des gehärteten Teils durch Fotopolymerisation geschmolzen, und anschließend wird ein Werkstück aus Metallpulver und lichtempfindlichem Harz hergestellt. In diesem Stadium ist das Metallpulver noch instabil, da die Dichte des Metallpulvers nicht hoch ist und ein zusätzliches Material, das Harz, vorhanden ist (dieser Zustand wird auch als Grünkörper bezeichnet).
Das erhaltene Werkstück wird im nächsten Prozess "entwachst und gesintert". In diesem Stadium wird das Harzmaterial geschmolzen und verflüchtigt (entfettet), und die verbleibenden Metallpulver werden agglomeriert und gesintert. Bei der LMM-Methode (und der Binder-Jet-Methode) ist dieser Sintervorgang ein wichtiger Prozess, der die Qualität des endgültigen Teils bestimmt, und Kenntnisse und Know-how in Bezug auf die Sinterung sind wichtig. Durch einen sorgfältig gesteuerten Entparaffinierungs- und Sinterungsprozess wird die Dichte des fertigen Metallteils auf 98 % oder mehr erhöht, und die Oberfläche wird so bearbeitet, dass eine Hochglanzpolitur möglich ist.
Zusammenfassend lässt sich sagen, dass bei der LMM-Methode Licht verwendet wird, um aus einem Gemisch aus lichtempfindlichem Harz und Metallpulver durch Fotopolymerisation einen Grünkörper zu formen, der nach dem Entparaffinierungs- und Sinterungsprozess die gleiche Metallmodellierung wie die MIM-Methode ergibt. Der Vorteil dieser Methode besteht darin, dass die Material- und Sintertechnologien von μ-MIM® direkt eingesetzt werden können, was für die Überprüfung nützlich ist. Da mit Licht gearbeitet wird, ist die Stapelung äußerst stabil und eine Teilegenauigkeit von ±0,2 % oder weniger ist möglich. Da das Werkstück nach der Formgebung ohne Kraftaufwand entnommen werden kann, ist es außerdem möglich, filigrane und komplexe Formen zu formen. Als Ergebnis kann eine mit μ-MIM® vergleichbare Qualität erreicht werden.
Vorteile von LMM
Drucken komplex geformter Komponenten
Es ist möglich, mikroskopisch kleine und komplex geformte Teile mit einer Qualität zu drucken, die der von μ-MIM® nahe kommt.
Nutzung der gleichen Ausrüstung und Technologie
Die gleichen Geräte und Technologien, die bei der μ-MIM®-Technologie eingesetzt werden, können auch bei diesem Verfahren verwendet werden.
Erreichen einer sehr hohen Präzision für Komponenten
Mit dieser Methode sind Toleranzen von weniger als 0,2 % möglich.
Zusammenarbeit zwischen 3D-Druck und μ-MIM®
Eines der Hindernisse für den Einsatz von μ-MIM® waren in der Vergangenheit die Vorlaufzeit und die Kosten bei der Prototypen- und Kleinserienfertigung. Mit der Erweiterung des 3D-Drucks von Metallen, die dem μ-MIM® entsprechen, als Option für unsere Kunden können wir Sie nun bereits in der Prototypen- und Kleinserienphase unterstützen - nicht nur mit der MIM-Technologie, sondern auch als Partner für Mikro- und komplex geformte Metallkomponenten.
Werfen Sie einen Blick auf einige mit 3D-Druck hergestellte Komponenten
Material
Größe
Zahnrad
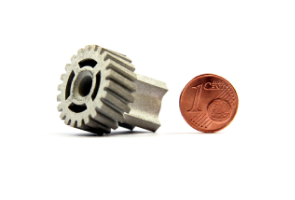
Rostfreier Stahl
φ15mm
Düse
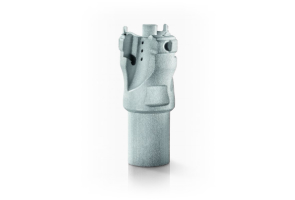
Titanlegierung
φ10×30mm
Vereinbaren Sie ein kostenloses Erstgespräch mit einem unserer Experten
Wir beantworten gerne Ihre offenen Fragen und zeigen Ihnen, wie wir Sie bei der Bewältigung Ihrer technischen Herausforderungen unterstützen können.