Es ist schon eine Weile her seit der Serie "Ich will es wissen, kann aber nicht fragen". In mehreren Ausgaben werden wir die Grundlagen, Realitäten und Probleme des Pulvers erörtern, das als Ausgangspunkt für die Fertigung nicht nur in der MIM-Industrie, sondern auch in verschiedenen anderen Branchen dient.
Mit wie vielen Pulverpartikeln haben wir es zu tun?
Lassen Sie uns mit einer groben Berechnung beginnen. Das von uns häufig verwendete Pulver mit einer durchschnittlichen Partikelgröße von etwa 8 μm hat etwa 2 Milliarden Partikel pro Kubikzentimeter. Wenn wir bei der Herstellung von Rohmaterial 5 kg Pulver verwenden und davon ausgehen, dass die Dichte von rostfreiem Stahl 7,8 g/cm3 beträgt, sind in dieser Menge etwa 1,25 Billionen Partikel enthalten. Außerdem ist kein Teilchen wie das andere.
Während die Weltbevölkerung etwa 8 Milliarden Menschen umfasst, arbeitet die MIM-Fertigung mit einem Kollektiv von Teilchen, das 150 Mal so groß ist. Ähnlich wie die Menschheit hat auch die MIM-Fertigung gelegentlich mit Störenfrieden zu tun und stellt Produkte her, während sie sich mit diesen Herausforderungen auseinandersetzt.
Bewertung des Pulvers
Das Ausgangsmaterial, ein entscheidendes Element bei der Herstellung von MIM, wird durch Erhitzen und Mischen von Metallpulver und Harzpulver hergestellt, wodurch eine lehmartige Masse entsteht, wie auf dem Foto unten zu sehen. Diese Masse wird dann in Form von Pellets verarbeitet, die als Ausgangsmaterial bezeichnet werden. Der gewünschte Formkörper wird durch Injektion dieses Ausgangsmaterials im Spritzgießverfahren hergestellt. Harzpulver ist zwar unverzichtbar, seine Bewertung ist jedoch schwierig, und es verbleibt nicht im Endprodukt. Daher liegt der Schwerpunkt bei MIM in erster Linie auf der Bewertung von Metallpulver.
Bei der Bewertung von Pulvern gibt es chemisch statische Bewertungen des Pulvers selbst, z. B. seine Form, Größe und Partikelgrößenverteilung. Es gibt auch chemisch-dynamische Bewertungen, wenn das Pulver mit einem Dispersionsmedium gemischt und in tatsächlichen Prozessen verwendet wird.Im Fall von MIM dient das Harzpulver als Dispersionsmedium, und die Ergebnisse der chemisch statischen Bewertung haben einen erheblichen Einfluss auf die Formbarkeit beim Gießen.
Es gibt auch chemisch-dynamische Bewertungen, wenn das Pulver mit einem Dispersionsmedium gemischt und in tatsächlichen Prozessen verwendet wird. Im Fall von MIM dient das Harzpulver als Dispersionsmedium, und die Ergebnisse der chemisch-statischen Bewertung haben einen erheblichen Einfluss auf die Formbarkeit während des Gießens.
Beim Kauf von Metallpulver gibt das Walzblatt Auskunft über die chemische Zusammensetzung, die Korngrößenverteilung (durchschnittliche Korngröße, D50-Wert) und die Klopfdichte. Die Schüttdichte ist zusammen mit dem Schüttwinkel das am besten geeignete Beurteilungskriterium für die Beurteilung von Pulver als Masse. Diese Ergebnisse, einschließlich der Schüttdichte, dienen als Indikatoren für die Vorhersage der Füllbarkeit, Mischbarkeit und Fließfähigkeit von Pulver.
Andererseits ist die Partikelgrößenverteilung die wichtigste Information bei der Handhabung von Pulver. Es gibt verschiedene Methoden zur Messung, aber es ist nicht übertrieben zu sagen, dass optische Messmethoden mit Lasern heutzutage der Mainstream sind. Das Gerät selbst ist teuer und kompliziert, aber der eigentliche Messvorgang besteht darin, eine Probe von der Größe eines Ohrstäbchens (ca. 0,1 g) in die Zelle zu geben, so dass es vielleicht das einfachste Verfahren ist. Außerdem ist es äußerst nützlich, weil es sofort eine "schöne" Verteilung und eine durchschnittliche Partikelgröße anzeigt, wie in der Abbildung oben zu sehen ist. Auch wenn man sich bei der Beurteilung des Pulvers, das in 25kg-Partien zu nur 0,1g gekauft wird, etwas unsicher fühlen könnte, zeigt das REM-Foto rechts oben, dass das gesamte Pulver tatsächlich von guter Qualität ist. (Fortsetzung folgt)
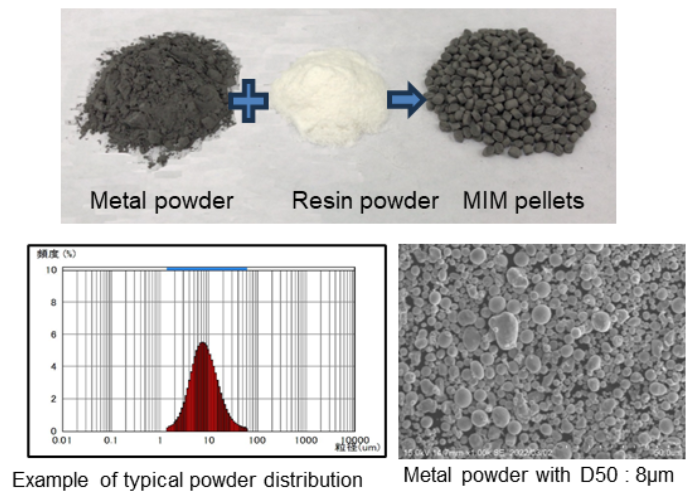
Wir werden auf der MD&M West 2024 in Anaheim, Kalifornien, USA zwischen dem6. und8. Februar 2024 an Stand Nr. 432 in Halle E im Anaheim Convention Center ausstellen. Bitte besuchen Sie unseren Stand auf der MD&M West!
Grüße aus Osaka, Japan
Hallo, ich bin Yukino Matsusue von der Abteilung Produktionskontrolle. Ich bin im April 2023 in das Unternehmen eingetreten und lerne jetzt, wie man die Produktionskosten kalkuliert und ein Prototypenprojekt plant usw. Ich freue mich, wenn die Projekte so gut laufen, wie wir es geplant haben, und wenn wir einen Auftrag für ein Angebot erhalten, an dessen Kalkulation ich beteiligt war. Ich versuche, meine Arbeit täglich zu genießen und gleichzeitig auf Details zu achten.
Mein Hobby ist es, leckeres Essen zu essen, vor allem Süßigkeiten, und ich habe im Sommer sehr gerne verschiedene Sorten Gelato gegessen. Am liebsten esse ich Pistazie und Himbeere.😋 Kürzlich habe ich Osechi (japanisches traditionelles Essen für die Neujahrstage) mit Süßigkeiten gegessen, das sehr lecker war.
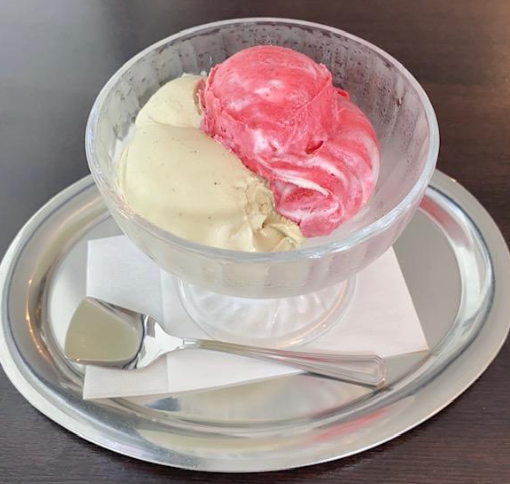
Download der PDF-Datei
Fazit
Risse, Absacken oder Blasenbildung werden häufig als Folge des Aufquellens des Bindemittels und/oder der unterschiedlichen Eigenspannungen zwischen der Oberfläche und dem Inneren beobachtet. Diese Probleme lassen sich durch die Auswahl geeigneter organischer Lösungsmittel und durch Temperaturkontrolle vermeiden.
Das katalytische Entbindern nutzt die Sublimation des Bindemittels, wodurch es möglich ist, das Bindemittel in relativ kurzer Zeit zu zersetzen und die Verformung zu minimieren. Bei einer stark sauren Atmosphäre ist die Auswahl an Metallwerkstoffen jedoch begrenzt.
Beim Sinterprozess setzt die Halsbildung („Necking“), d. h. die Ausbildung von Brückenbindungen zwischen Metallpulverkörnern durch thermische Diffusion, bei Erreichen der Sintertemperatur ein. Sobald dieses Necking einsetzt, wird eine Schrumpfung beobachtet, die die Dichte erhöht. Bevor das Necking einsetzt, sollten daher alle organischen Bestandteile zersetzt und das Gas zwischen den Pulverkörnern entfernt werden. Im Sinterprozess führen unerwünschte chemische Reaktionen wie Oxidation oder Karbonisierung zum Verlust mechanischer Eigenschaften, weshalb zu Beginn des Prozesses eine präzise Atmosphärensteuerung mit niedriger Heizrate erforderlich ist. Wenn die Sintertemperatur erreicht ist, können außerdem einige pflanzenbasierte Bindemittel verdampfen.