μ-MIM® Technical Newsletter Vol. 34: Qualitätssicherung von μ-MIM
Im Vergleich zu anderen Verfahren zur Herstellung von Metallkomponenten ist das Metall-Spritzgussverfahren (MIM) ziemlich kompliziert und jeder Prozessschritt ist interaktiv. Außerdem werden bei unserer μ-MIM-Technologie in der Regel sehr komplex gestaltete kleine Bauteile in Serienproduktion hergestellt. Daher ist eine besonders strenge Qualitätskontrolle in und um die Produktionslinie erforderlich, um die Anforderungen der Kunden zu erfüllen. Dieses Mal werden wir unsere Qualitätssicherung vorstellen.
MIM-Prozess und Qualitätskontrolle
MIM-Verfahren lassen sich in fünf Prozesse unterteilen, nämlich 1) Herstellung des Ausgangsmaterials, 2) Spritzgießen, 3) Entbindern und Sintern, 4) zusätzliche Nachbearbeitung und 5) Messen und Prüfen.
In Prozess 1) wird die Materialkontrolle sowohl bei Metallpulver als auch bei Bindemitteln an erster Stelle genannt. Bei der Eingangskontrolle von Metallpulver werden nicht nur die chemische Zusammensetzung des Pulvers, sondern auch die Größenverteilung des Pulvers und seine Form gemessen. Wichtig ist auch die Kontrolle der Lagerung des Metallpulvers und des Bindemittels. Bei ungeeigneten Lagerungsbedingungen schreitet die Zersetzung der Materialien schneller voran und führt zu schlechten mechanischen Eigenschaften der gesinterten Bauteile. Das MIM-Feedstock-Pellet wird mit Hilfe von Knet- und Pelletiermaschinen hergestellt. Während des Knetvorgangs sollte eine ausreichende Scherbeanspruchung auf das Ausgangsmaterial mit erhöhter Temperatur ausgeübt werden, um eine gleichmäßige Verteilung des Metallpulvers im Ausgangsmaterial zu erreichen. Gleichzeitig ist eine sorgfältige Temperaturbeobachtung des Ausgangsmaterials erforderlich. Wenn es überhitzte Bereiche gibt, schreitet der thermische Abbau des Bindemittels voran und die Produktivität wird erheblich beeinträchtigt. Außerdem sind unsere μ-MIM-Komponenten meist recht klein, und das Volumen der Komponente kann kleiner sein als das eines Pellets. Daher ist die Gleichmäßigkeit des Ausgangsmaterials einer der wichtigsten Punkte bei der Qualitätskontrolle, so dass wir besonders gut auf die Qualität jedes einzelnen Pellets achten.
Bei 2), dem Spritzgussverfahren, wird die höchste Belastung auf das Ausgangsmaterial ausgeübt. Aufgrund der hohen Belastung bei erhöhten Temperaturen kann es zu einem unerwarteten Abbau des Bindemittels kommen. Da wir den Anguss oder die fehlgeschossenen Grünteile recyceln, wird das Ausgangsmaterial während des Spritzgießens ebenfalls genau beobachtet. Wir erhalten ein stabiles Volumen der Grünteile nach dem Spritzgießprozess, so dass eine präzise Gewichtsmessung für die Qualitätsbewertung von Grünteilen im Allgemeinen eingesetzt wird. Zur Verbesserung der Materialausbeute wird auch die Erscheinungsbildkontrolle durchgeführt. Die endgültige Bauteilqualität wird durch 3) den Entbinderungs- und Sinterungsprozess bestimmt. Der Entbinderungsprozess kann in 2 Schritten, 1. und 2. Entbinderung, in den verschiedenen Öfen durchgeführt werden. Beim 1. Entbindern wird der größte Teil des Bindemittels zersetzt, so dass die organische Verunreinigung im Ofen wahrscheinlich ist. Beim 2. Entbindern ist nur noch ein kleiner Teil des Bindemittels vorhanden, der die Form der Metallpulverpartikel unterstützt, und dieser kleine Teil des Bindemittels wird bei höheren Temperaturen als beim 1. Im Allgemeinen wird diese 2. Entbinderung im Sinterofen durchgeführt.
Es gibt viele MIM-Hersteller, die das erste und zweite Entbindern in getrennten Öfen durchführen, aber wir, μ-MIM, führen alles in einem Prozess durch. Der 1-Ofen-Betrieb erfordert eine gute atmosphärische Kontrolle während des Entbinderungsprozesses, verglichen mit dem Betrieb in getrennten Öfen. Daher ist der Preis des Ofens viel höher als bei der getrennten Variante. Unser System kann jedoch einen Verlust durch die Handhabung zwischen dem Entbinderungs- und dem Sinterprozess vermeiden, da die nach dem 1. entbinderten Teil sehr zerbrechlich sind. Im Sinterprozess wird eine lineare Schrumpfung von mehr als 10% durch thermische Diffusion zwischen den Metallpulvern beobachtet. Daher ist eine geeignete Auswahl der Keramikplatten erforderlich, z. B. in Bezug auf Material, Porosität, Design, Betriebsbedingungen usw., um eine stabile Qualität in der Serienproduktion zu erreichen.
Unter 4) Sekundärprozesse können die Oberflächenveredelung (Sandstrahlen, Trowalisieren, Galvanisieren), die spanende Bearbeitung (Gewindeschneiden, Prägen) und die thermische Behandlung (Aushärtung, Ausscheidungshärtung) aufgeführt werden. Pulvermetallurgische Bauteile weisen aufgrund des Metallpulvers einen gewissen Grad an Rauheit auf, jedoch wird in der Nachbearbeitung das gleiche Endbearbeitungsniveau wie bei zerspanten Bauteilen erreicht. Als letzter Prozess umfasst die 5) Auslieferungsinspektion die visuelle Inspektion des Aussehens, die Toleranzinspektion mittels Mikrometer, optisches 3D-Messsystem, Röntgen-CT, und einige Messungen der chemischen Zusammensetzung mittels SEM-EDX, Verbrennungstest.
ISO13485-zertifizierte Qualitätssicherung
Das Qualitätssicherungssystem von μ-MIM ist nach ISO 13485 zertifiziert, da die Nachfrage in der Medizinprodukteindustrie ständig steigt. Wie bereits erwähnt, gibt es je nach Prozessschritt viele Kontrollwerte und -punkte, die durch das Design des Bauteils multipliziert werden. Wir verbessern unser Qualitätssicherungssystem ständig, da sich die Messtechnik weiterentwickelt.
Säule
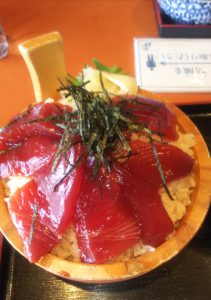
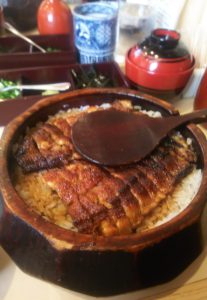
Hallo, ich bin Sakai und arbeite in der Produktionsabteilung. Ich bin für das Spritzgießen und die interne Systemverwaltung zuständig. Ich arbeite seit 7 Jahren und habe das Gefühl, dass sich die Informationstechnologie durch meine Arbeit in der Systemsteuerung stark weiterentwickelt hat. Auch beim Spritzgießen sind die Spritzgussmaschinen dieselben wie früher, aber die Spritzgussteile sind komplexer geworden.
An den Wochenenden schaue ich gerne Sport. Früher besuchte ich die Wettkämpfe vor Ort, um meine Lieblingsmannschaft anzufeuern, aber heute sehe ich mir diese Spiele zu Hause im Fernsehen an. Vor kurzem habe ich den Ise-Schrein und den Atsuta-Schrein besucht, um für eine baldige Rückkehr zur Normalität zu beten. Auf dem Rückweg von den Schreinen habe ich auch die lokalen Gerichte genossen.
Fazit
Risse, Absacken oder Blasenbildung werden häufig als Folge des Aufquellens des Bindemittels und/oder der unterschiedlichen Eigenspannungen zwischen der Oberfläche und dem Inneren beobachtet. Diese Probleme lassen sich durch die Auswahl geeigneter organischer Lösungsmittel und durch Temperaturkontrolle vermeiden.
Das katalytische Entbindern nutzt die Sublimation des Bindemittels, wodurch es möglich ist, das Bindemittel in relativ kurzer Zeit zu zersetzen und die Verformung zu minimieren. Bei einer stark sauren Atmosphäre ist die Auswahl an Metallwerkstoffen jedoch begrenzt.
Beim Sinterprozess setzt die Halsbildung („Necking“), d. h. die Ausbildung von Brückenbindungen zwischen Metallpulverkörnern durch thermische Diffusion, bei Erreichen der Sintertemperatur ein. Sobald dieses Necking einsetzt, wird eine Schrumpfung beobachtet, die die Dichte erhöht. Bevor das Necking einsetzt, sollten daher alle organischen Bestandteile zersetzt und das Gas zwischen den Pulverkörnern entfernt werden. Im Sinterprozess führen unerwünschte chemische Reaktionen wie Oxidation oder Karbonisierung zum Verlust mechanischer Eigenschaften, weshalb zu Beginn des Prozesses eine präzise Atmosphärensteuerung mit niedriger Heizrate erforderlich ist. Wenn die Sintertemperatur erreicht ist, können außerdem einige pflanzenbasierte Bindemittel verdampfen.