μ-MIM® Technical Newsletter Vol. 32: Problemlösungen im MIM-Verfahren; Spritzgießverfahren
Beim Metall-Spritzgießen (MIM) beeinflusst jeder Verarbeitungsparameter die Qualität des endgültigen Bauteils erheblich, insbesondere bei der Herstellung kleiner und kompliziert konstruierter MIM-Bauteile. Dieses Mal möchten wir einige häufige Fehler und ihre Lösung im Spritzgussverfahren vorstellen.
Lösung von Einspritzproblemen beim Formenbau
Eines der Alleinstellungsmerkmale von MIM ist die endkonturnahe Serienfertigung. Daher versuchen die MIM-Hersteller stets, die Nachbearbeitung zu minimieren. Hinzu kommt, dass die kleinen Bauteile, mit denen wir es bei μ-MIM® zu tun haben, im Bearbeitungsprozess schwer zu halten oder zu spannen sind. Daher ist es notwendig, den Nachbearbeitungsabschnitt zu eliminieren. Im Allgemeinen ist der Spritzgussprozess der einzige Schritt, bei dem das Bauteil geformt wird; daher ist es wichtig, die Form so zu gestalten, dass die Möglichkeit der Nachbearbeitung ausgeschlossen oder minimiert wird. Die Anschnittkonstruktion wirkt sich am stärksten auf die Bauteilqualität im Spritzgießschritt aus. Die größte Scherspannungsänderung am Ausgangsmaterial tritt am Anschnitt auf, d. h. die höchste Anteilsspannung wird am Anschnitt und die niedrigste Anteilsspannung kurz nach dem Passieren des Anschnittbereichs beobachtet. Diese Scherspannungsänderung führt zur Entmischung von Metallpulver und Bindemittel und schließlich zu einer schlechten Oberflächenqualität, Verformung und inhomogener Dichte des Teils. Die Lösung für dieses Problem besteht darin, den Anschnitt mit großem Querschnitt an der dicksten Stelle des Bauteils anzubringen. Die meisten Kunden sind jedoch nicht glücklich darüber, einen großen Anschnitt zu haben, und sie könnten eine Nachbehandlung für den großen hässlichen Anschnitt verlangen. Eine Vergrößerung der Anschnittfläche ist daher aus optischen Gründen nicht sinnvoll, und außerdem beeinträchtigt der große Anschnitt die Produktivität, da der Anschnitt, d. h. die Entnahme des Teils aus dem Anguss, schwierig ist.
Problemlösung bei den Formparametern
Die Gestaltung des Luftstroms in der Form ist ebenfalls wichtig für ein stabiles Spritzgießen. Der Spritzgießprozess findet normalerweise bei atmosphärischem Druck statt. Wenn das Material in der Kavität ankommt, verbleibt also etwas Luft. Die verbleibende Luft sollte aus der Kavität verdrängt werden, ohne den Druck auf das Material zu erhöhen, wenn das Werkzeug vollständig geschlossen ist. Leider ist der Luftstrom und die Gratbildung ein Kompromissverhältnis. Die Optimierung der Einspritzparameter ist auch für eine stabile Serienproduktion von Nutzen. Bei der idealen kleinen Anschnittgröße mit minimalem Werkzeugabstand sind Schwierigkeiten bei der Einspritzung zu erwarten, jedoch kann eine niedrigere Einspritzgeschwindigkeit die Änderung der Anteilsspannung minimieren und eine gute Luftströmung ohne Gratbildung gewährleisten. Andererseits führt eine niedrige Einspritzgeschwindigkeit zu Bindenähten oder Fließspuren aufgrund der niedrigen Viskosität des Ausgangsmaterials. Wenn die Einspritzgeschwindigkeit niedrig ist, dauert es länger, bis das Material in die Kavität fließt, und die Temperatur des Materials sinkt. Das Futtermittel mit niedriger Temperatur hat eine hohe Viskosität, und es entstehen Bindenähte oder Fließspuren, die nicht nur zu Problemen mit dem Aussehen, sondern auch mit den mechanischen Eigenschaften führen.
Die Entwicklung von Rohstoffen vergrößert das Fenster für die Injektionsverarbeitung
Wie bereits erwähnt, ist das Abgleichen von Parametern eine wichtige Technik zur Realisierung einer stabilen Serienproduktion. Da wir seit mehr als 50 Jahren Erfahrung mit dem Spritzgussverfahren haben, einschließlich der Ära des Kunststoffspritzgusses, sind wir zuversichtlich, was die Optimierung der Einspritzparameter angeht. Doch selbst wenn wir in unsere Erfahrung mit dem Kunststoffspritzguss investieren, ist das MIM-Spritzgießen schwierig, und das Gießen kleiner, komplizierter MIM-Bauteile ist noch schwieriger. Der Grund dafür, dass μ-MIM® die Serienproduktion von kleinen, komplizierten Designkomponenten realisiert hat, ist, dass wir auch das Ausgangsmaterial weiterentwickelt haben. Wir sind in der Lage, die Problempunkte zu spezifizieren, die wir bei der Optimierung der Spritzgießparameter nicht beseitigen können, und die Problempunkte bei der Entwicklung des Ausgangsmaterials zu berücksichtigen. Unsere μ-MIM®-Technologie wird Ihr MIM-Verständnis herausfordern.
Säule
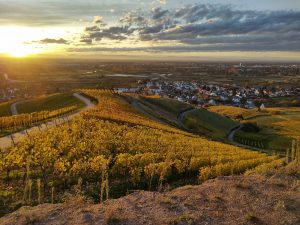
Das Gebiet, in dem sich unser europäisches Büro befindet, heißt Ortenaukreis und liegt im Bundesland Baden-Württemberg, im Südwesten Deutschlands. Sie ist als Weinanbaugebiet sehr bekannt. Es gibt eine Route namens Badische Weinstraße, die sich über 200 km erstreckt! Im Herbst gibt es Weinfeste und Weinwanderungen in verschiedenen Städten, darunter auch in Offenburg, wo sich unser Büro befindet. Leider haben wir wegen der COVID-Pandemie in den Jahren 2020 und 2021 kein Weinfest, aber hoffentlich können Sie uns nächstes Jahr in dieser Zeit besuchen. Jetzt ist das Weinfeld in goldener Farbe, was absolut erstaunlich ist!
Fazit
Risse, Absacken oder Blasenbildung werden häufig als Folge des Aufquellens des Bindemittels und/oder der unterschiedlichen Eigenspannungen zwischen der Oberfläche und dem Inneren beobachtet. Diese Probleme lassen sich durch die Auswahl geeigneter organischer Lösungsmittel und durch Temperaturkontrolle vermeiden.
Das katalytische Entbindern nutzt die Sublimation des Bindemittels, wodurch es möglich ist, das Bindemittel in relativ kurzer Zeit zu zersetzen und die Verformung zu minimieren. Bei einer stark sauren Atmosphäre ist die Auswahl an Metallwerkstoffen jedoch begrenzt.
Beim Sinterprozess setzt die Halsbildung („Necking“), d. h. die Ausbildung von Brückenbindungen zwischen Metallpulverkörnern durch thermische Diffusion, bei Erreichen der Sintertemperatur ein. Sobald dieses Necking einsetzt, wird eine Schrumpfung beobachtet, die die Dichte erhöht. Bevor das Necking einsetzt, sollten daher alle organischen Bestandteile zersetzt und das Gas zwischen den Pulverkörnern entfernt werden. Im Sinterprozess führen unerwünschte chemische Reaktionen wie Oxidation oder Karbonisierung zum Verlust mechanischer Eigenschaften, weshalb zu Beginn des Prozesses eine präzise Atmosphärensteuerung mit niedriger Heizrate erforderlich ist. Wenn die Sintertemperatur erreicht ist, können außerdem einige pflanzenbasierte Bindemittel verdampfen.