μ-MIM® Technical Newsletter Vol. 33: Problemlösungen im MIM-Prozess; Entbinderungs- und Sinterungsprozess
In der letzten Ausgabe des Jahres 2021 möchten wir einige häufige Fehler und Problemlösungen beim Entbinderungs- und Sinterungsprozess beim Metall-Spritzgießen (MIM) vorstellen.
Die häufigsten Fehler beim MIM-Entbinderungsprozess
Das Bindemittel in der Pulvermetallurgie ist ein elementares Material, das dem Metallpulver die Fließfähigkeit in der Form verleiht. Vor allem in der MIM-Metallurgie ist die Konstruktion in der Regel komplizierter als in der Verdichtungsmetallurgie, daher wird das 10-fache oder ein größeres Volumen des Binders in der Verdichtungsmetallurgie in das MIM-Rohmaterial (Werkstoff) gemischt. Allerdings kann keine der mit dem Binder verbundenen Zusammensetzungen im endgültigen Bauteil verbleiben, so dass der Binder im Entbinderungs- und Sinterungsprozess vollständig zersetzt werden sollte. Der größte Teil des Bindemittels sollte im Entbinderungsprozess abgebaut werden, während im Sinterprozess nur eine sehr geringe Menge des Bindemittels abgebaut wird. Das liegt daran, dass das Bindemittel bis zum Beginn des Sinterns auch als Stütze der Bauteilform dient.
Während des Entbinderungs- und Sinterungsprozesses treten in der Regel einige optische Mängel auf, wie z. B. Risse, Verformungen, Verwerfungen, Blasen und der Verlust mechanischer Eigenschaften durch Veränderungen der chemischen Zusammensetzung.
Problemlösung bei den Formparametern
Die Gestaltung des Luftstroms in der Form ist ebenfalls wichtig für ein stabiles Spritzgießen. Der Spritzgießprozess findet normalerweise bei atmosphärischem Druck statt. Wenn das Material in der Kavität ankommt, verbleibt also etwas Luft. Die verbleibende Luft sollte aus der Kavität verdrängt werden, ohne den Druck auf das Material zu erhöhen, wenn das Werkzeug vollständig geschlossen ist. Leider ist der Luftstrom und die Gratbildung ein Kompromissverhältnis. Die Optimierung der Einspritzparameter ist auch für eine stabile Serienproduktion von Nutzen. Bei der idealen kleinen Anschnittgröße mit minimalem Werkzeugabstand sind Schwierigkeiten bei der Einspritzung zu erwarten, jedoch kann eine niedrigere Einspritzgeschwindigkeit die Änderung der Anteilsspannung minimieren und eine gute Luftströmung ohne Gratbildung gewährleisten. Andererseits führt eine niedrige Einspritzgeschwindigkeit zu Bindenähten oder Fließspuren aufgrund der niedrigen Viskosität des Ausgangsmaterials. Wenn die Einspritzgeschwindigkeit niedrig ist, dauert es länger, bis das Material in die Kavität fließt, und die Temperatur des Materials sinkt. Das Futtermittel mit niedriger Temperatur hat eine hohe Viskosität, und es entstehen Bindenähte oder Fließspuren, die nicht nur zu Problemen mit dem Aussehen, sondern auch mit den mechanischen Eigenschaften führen.
Problemlösungen bei der Entbinderung und Sinterung
Beim Entbinderungsprozess werden thermische, organische Lösungsmittel und katalytische Reaktionen zur Zersetzung des Bindemittels eingesetzt. Die thermische Zersetzung ist die einfachste, aber zeitaufwendigste Methode. Die laminare Strömung im Ofen verbessert die Effizienz, da sich das zersetzte Bindemittel in der Gasphase befindet. Das Bindemittel wird in einem bestimmten Temperaturbereich nacheinander zersetzt, so dass bei einer zu hohen Temperaturerhöhungsrate häufig eine Blasenbildung zu beobachten ist.
Beim Lösungsmittel-Entbindern wird der Grünling in ein flüssiges oder dampfförmiges Lösungsmittel getaucht, um das Bindemittel zu zersetzen. Aufgrund der Quellung des Bindemittels und/oder des Eigenspannungsunterschieds zwischen der Oberfläche und dem Inneren kommt es häufig zu Rissbildung, Absacken oder Blasenbildung. Diese Probleme lassen sich durch die Auswahl geeigneter organischer Lösungsmittel und durch Temperaturkontrolle vermeiden.
Das katalytische Entbindern nutzt die Sublimation des Bindemittels, wodurch es möglich ist, das Bindemittel in relativ kurzer Zeit zu zersetzen und die Verformung zu minimieren. Bei einer stark sauren Atmosphäre ist die Auswahl an geeigneten Metallwerkstoffen jedoch begrenzt.
Beim Sinterprozess beginnt die Einschnürung, die die Metallpulver durch thermische Diffusion überbrückt, bei der Sintertemperatur. Sobald die Einschnürung einsetzt, wird eine Schrumpfung beobachtet, die die Dichte erhöht. Bevor die Einschnürungsreaktion einsetzt, sollten daher alle organischen Bestandteile zersetzt und das Gas zwischen den Pulvern entfernt werden. Im Sinterprozess führen unerwünschte chemische Reaktionen wie Oxidation oder Karbonisierung zum Verlust mechanischer Eigenschaften, weshalb zu Beginn des Prozesses eine präzise Atmosphärensteuerung mit niedriger Heizrate erforderlich ist. Außerdem kann bei Erreichen der Sintertemperatur ein Teil des zugesetzten Metalls verdampfen. Daher ist auch hier die Kontrolle der Atmosphäre wichtig, um den Verlust des Zusatzmetalls zu minimieren und die Eigenschaften der Legierung zu erhalten. Um den Verlust des Zusatzmetalls zu vermeiden, wird in einigen Fällen das Sintern in einer Inertgasatmosphäre durchgeführt.
μ-MIM®︎ Entbinderungs- und Sinterungstechnik
In unserem μ-MIM®︎-Verfahren verwenden wir hauptsächlich das thermische Entbindern mit einem 2-in-1-Ofen, so dass der Entbinderungs- und Sinterungsprozess in einem Ofen durchgeführt werden kann. Für die Herstellung hochwertiger Sinterteile ist eine genaue und präzise atmosphärische Kontrolle erforderlich, daher haben wir mit dem Ofenhersteller zusammengearbeitet, um den 2-in-1-Ofen zu entwickeln. Dieser Ofen ist entscheidend für eine stabile Serienproduktion von kleinen, kompliziert gestalteten MIM-Teilen. Außerdem wird unsere Entbinderungs- und Sintertechnologie im Bereich der additiven Fertigung eingesetzt.
Bitte überlassen Sie uns Ihre Entbinderungs- und Sinterungsprobleme.
Referenz: Handbuch des Metall-Spritzgießens Zweite Auflage (ISBN: 978-0-08-102152-1)
Säule
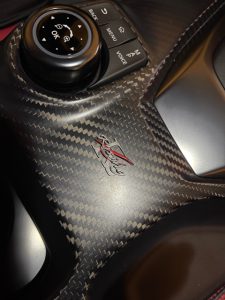
Hallo. Ich bin Sumiyo Morita, verantwortlich für die Verwaltung und die Buchhaltung. Ich arbeite hier schon länger als alle anderen Mitarbeiter, mit Ausnahme unseres Firmenchefs. Da ich über viel Erfahrung im Unternehmen verfüge, sorge ich dafür, dass die gemeinsamen Anstrengungen des Teams zu einem reibungslosen Ergebnis führen. Ich komme nicht aus dem technischen Bereich, aber im Laufe der Zeit habe ich mich mit den technischen Aspekten meiner Arbeit sowie mit den Bedürfnissen und Erwartungen der Kunden vertraut gemacht. Ich bin ein Theaterbesucher, und die Wiedereröffnung von Theatern macht mich glücklich, auch wenn sie noch begrenzt ist. Heutzutage interessiere ich mich auch für Autorennen. Glücklicherweise bin ich mit einem professionellen Rennfahrer befreundet und habe die Möglichkeit, ihn durch die Lieferung seines mit unserer 3D-Drucktechnologie hergestellten Logos zu unterstützen.
Fazit
Risse, Absacken oder Blasenbildung werden häufig als Folge des Aufquellens des Bindemittels und/oder der unterschiedlichen Eigenspannungen zwischen der Oberfläche und dem Inneren beobachtet. Diese Probleme lassen sich durch die Auswahl geeigneter organischer Lösungsmittel und durch Temperaturkontrolle vermeiden.
Das katalytische Entbindern nutzt die Sublimation des Bindemittels, wodurch es möglich ist, das Bindemittel in relativ kurzer Zeit zu zersetzen und die Verformung zu minimieren. Bei einer stark sauren Atmosphäre ist die Auswahl an Metallwerkstoffen jedoch begrenzt.
Beim Sinterprozess setzt die Halsbildung („Necking“), d. h. die Ausbildung von Brückenbindungen zwischen Metallpulverkörnern durch thermische Diffusion, bei Erreichen der Sintertemperatur ein. Sobald dieses Necking einsetzt, wird eine Schrumpfung beobachtet, die die Dichte erhöht. Bevor das Necking einsetzt, sollten daher alle organischen Bestandteile zersetzt und das Gas zwischen den Pulverkörnern entfernt werden. Im Sinterprozess führen unerwünschte chemische Reaktionen wie Oxidation oder Karbonisierung zum Verlust mechanischer Eigenschaften, weshalb zu Beginn des Prozesses eine präzise Atmosphärensteuerung mit niedriger Heizrate erforderlich ist. Wenn die Sintertemperatur erreicht ist, können außerdem einige pflanzenbasierte Bindemittel verdampfen.