μ-MIM® Technical Newsletter Vol. 28: Pulverunterschiede durch Pulverherstellungsverfahren
In diesem Newsletter stellen wir die Unterschiede zwischen den Metallpulvern für die Herstellung von MIM-Bauteilen vor. In Ausgabe 11 sprachen wir über Titanpulver, und dieses Mal geht es um Eisen- oder Edelstahlpulver, das am häufigsten beim Metallspritzguss oder der MIM-Produktion verwendet wird.
Erforderliche Spezifikationen für MIM-Pulver
Eine durchschnittliche Pulververteilungsgröße (D50) von 10 μm ist auf dem Markt für Metallspritzguss (MIM) üblich, was in der pulvermetallurgischen Industrie ein kleinerer Bereich ist. Darüber hinaus wirkt sich auch die Form des Pulvers selbst auf die Produktivität aus; daher ist kugelförmiges kleines Pulver die günstigste Pulverspezifikation beim Metallspritzguss. Der Zerstäubungsprozess kann in 2 Arten unterteilt werden, je nach Kühlmedium, Wasser- oder Gaszerstäubungspulver. Im Falle von Titanpulver ist die Reaktivität gegenüber Sauerstoff in Wasser bei erhöhter Temperatur extrem hoch, so dass die Wasser-Gas-Zerstäubung nicht angewendet wird. Eisenhaltige Pulver, insbesondere Edelstahlpulver, werden jedoch im Wasserverdüsungsverfahren hergestellt. Die Wasserverdüsung bei der Herstellung von rostfreiem Stahl wird seit den 1950er Jahren erforscht und entwickelt.
Der Unterschied zwischen wasser- und gaszerstäubtem Pulver
Diese SEM-Bilder zeigen gaszerstäubtes (links) und wasserzerstäubtes (rechts) Pulver. Wie auf den Bildern zu sehen ist, ist die Pulvergröße fast gleich, aber die Form ist unterschiedlich.
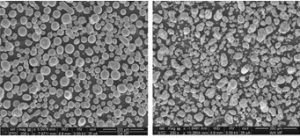
Das wasserzerstäubte Pulver hat einen höheren Sauerstoffgehalt und eine größere Vielfalt an Pulverformen, weshalb es sich nicht für die additive Fertigung von Metallen eignet. Das wasserzerstäubte Pulver gewinnt jedoch aufgrund der stabilen und niedrigen Produktionskosten wieder an Aufmerksamkeit, da der Preis für Edelgas, das bei der Herstellung von gaszerstäubtem Pulver entscheidend ist, steigt. Außerdem ist die Abkühlungsrate bei der Wasserzerstäubung viel schneller als bei der Gaszerstäubung. Daher gewinnt die Wasserzerstäubung bei der Herstellung von amorphen Legierungen, rostfreiem Stahl neuer Zusammensetzung oder anderen Legierungspulvern, die eine Kontrolle der Mikrostruktur erfordern, zunehmend an Bedeutung.
Zukunft des atomisierten Pulvers
Die Produktionskapazitäten für zerstäubtes Metallpulver nehmen weltweit zu, um die steigende Nachfrage der additiven Fertigungsindustrie zu befriedigen. Die Metallpulverhersteller haben in modernste Zerstäubungsanlagen investiert, die eine hohe Produktivität und Qualität gewährleisten. Es ist einfacher als noch vor einigen Jahren, hochwertiges Pulver zu kaufen. Daher glauben wir, dass die Anforderungen an unsere Anwendung der Mikro-Metall-Spritzguss- oder (μ-MIM®)-Technologie immer mehr zunehmen werden. Wenn Sie die Massenproduktion Ihrer kleinen, kompliziert gestalteten Metallteile in Erwägung ziehen, nehmen Sie bitte Kontakt mit uns auf.
Referenzen
https://doi.org/10.1016/j.addma.2020.101675
https://www.pim-international.com/powder-injection-moulding-international-magazine-archive/pim-international-vol-13-no-1-march-2019/
http://www.atmix.co.jp/pdf/201014.pdf
Säule
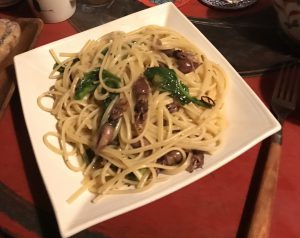
Ich bin Ryoichi Wada, der seit letztem Sommer in der F&E-Abteilung arbeitet. Sowohl in meiner vorherigen Position als auch in meinem Studium habe ich mich auf Polymere spezialisiert. Meine Mission in Bezug auf die Arbeit ist "auch Spaß an der Arbeit zu haben!" und ich möchte eine Person sein, die das Team hinter den Kulissen unterstützen kann, wie der Binder im MIM-Prozess. Ich liebe es, neue Dinge zu lernen, und mein derzeitiges Hobby ist es, mit Energie x Zeit x Katalysator (Gewürze) ein köstliches Gericht mit saisonalen Zutaten zuzubereiten. Ich habe mich gefreut, dass es mir gelungen ist, ein leckeres Nudelgericht mit Glühwürmchen-Tintenfisch und Rapsblüten zuzubereiten, die jetzt Saison haben.
Fazit
Risse, Absacken oder Blasenbildung werden häufig als Folge des Aufquellens des Bindemittels und/oder der unterschiedlichen Eigenspannungen zwischen der Oberfläche und dem Inneren beobachtet. Diese Probleme lassen sich durch die Auswahl geeigneter organischer Lösungsmittel und durch Temperaturkontrolle vermeiden.
Das katalytische Entbindern nutzt die Sublimation des Bindemittels, wodurch es möglich ist, das Bindemittel in relativ kurzer Zeit zu zersetzen und die Verformung zu minimieren. Bei einer stark sauren Atmosphäre ist die Auswahl an Metallwerkstoffen jedoch begrenzt.
Beim Sinterprozess setzt die Halsbildung („Necking“), d. h. die Ausbildung von Brückenbindungen zwischen Metallpulverkörnern durch thermische Diffusion, bei Erreichen der Sintertemperatur ein. Sobald dieses Necking einsetzt, wird eine Schrumpfung beobachtet, die die Dichte erhöht. Bevor das Necking einsetzt, sollten daher alle organischen Bestandteile zersetzt und das Gas zwischen den Pulverkörnern entfernt werden. Im Sinterprozess führen unerwünschte chemische Reaktionen wie Oxidation oder Karbonisierung zum Verlust mechanischer Eigenschaften, weshalb zu Beginn des Prozesses eine präzise Atmosphärensteuerung mit niedriger Heizrate erforderlich ist. Wenn die Sintertemperatur erreicht ist, können außerdem einige pflanzenbasierte Bindemittel verdampfen.