μ-MIM® Technical Newsletter Vol. 37: Unsere Metall-3D-Drucktechnologie
Wie bereits in unserem technischen Newsletter und in unseren Webinaren angekündigt, nimmt unser Metall-3D-Drucker nun den Vollbetrieb auf. Das Drucksystem wurde bisher mit einem Punktdurchmesser von 35 µm betrieben und ist nun mit einem speziellen 15-µm-Punkt erhältlich.
Einführung des lang erwarteten Systems mit 15μm Spotdurchmesser
Um den Zeitraum für das Prototyping von μ-MIM-Bauteilen zu verkürzen, verwenden wir seit letztem Sommer den 3D-Drucker LMM (Lithography-based Metal Manufacturing) der Incus GmbH für vorläufige Prototypen. Das Fehlen eines Prototyping-Systems im Haus hatte zuvor zu einer komplizierten Verwaltung vertraulicher Informationen und langen Prototyping-Zeiten geführt. Durch die Einführung des LMM-3D-Druckers konnten wir jedoch erheblich Zeit einsparen. Wir haben die Einführung des Drucksystems mit einem Spotdurchmesser von 15 µm erfolgreich abgeschlossen, mit dem Bauteile mit einer Maßtoleranz und Oberflächenbeschaffenheit hergestellt werden können, die näher an der Qualität von Bauteilen liegt, die mit der μ-MIM-Technologie hergestellt wurden. Obwohl die Pandemievorschriften den Besuch eines Ingenieurs der Incus GmbH aus Österreich in Japan behinderten, konnten wir Ende April den Druck in vollem Umfang in Betrieb nehmen.
Metall-3D-Drucker mit der LMM-Methode belichten ein Gemisch aus lichtempfindlichem Harz und Metallpulver mit einer bestimmten Wellenlänge, um durch eine Polymerisationsreaktion Bauteile präzise zu formen, und die geformten Bauteile werden nach dem Entbinderungs- und Sinterungsprozess zu Metallteilen. Beim Entbinderungs- und Sinterungsprozess von LMM-Bauteilen können dieselben Geräte und Technologien wie bei der μ-MIM-Technologie eingesetzt werden. Da das lichtempfindliche Harz, das beim 3D-Metalldruck verwendet wird, eine andere Zusammensetzung hat als das Bindemittel, das beim MIM verwendet wird, müssen für die LMM-Formteile optimierte Prozessbedingungen beim Entbinderungsprozess eingehalten werden, während die Sinterbedingungen die gleichen sind wie beim μ-MIM. Mit anderen Worten, wir sind in der Lage, Ihnen Prototypen mit kurzen Lieferzeiten anzubieten, indem wir das gleiche Metallpulver und die gleiche Sintertechnologie wie bei μ-MIM verwenden. Außerdem können wir durch die Einführung eines Spotdurchmessers von 15 µm Formteile herstellen, die näher an die von μ-MIM herankommen.
Andererseits weisen Prototypen für den 3D-Druck aus Metall andere Aspekte auf als Prototypen aus μ-MIM, z. B. eine geringe Oberflächenrauheit, eine Begrenzung der dünnen Wandstruktur (200 μm an der dünnsten Stelle, weniger als 100 μm bei μ-MIM) und eine Anisotropie der mechanischen Festigkeit je nach Stapelrichtung, die bei 3D-Druckern aus Metall unvermeidlich ist. Daher erläutern wir unseren Kunden diese Punkte für jede Bauteilzeichnung vor dem Prototyping.
Beispiel: Vergleich des Spotdurchmessers und des Spalts
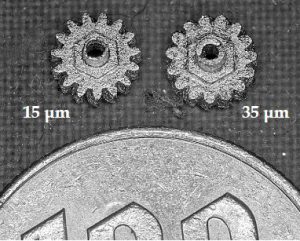
Die linke Abbildung zeigt Zahnradproben mit einem Außendurchmesser von ca. 4 mm, die nach der Formgebung mit einem Punktdurchmesser von 15 µm und 35 µm entbindert und gesintert wurden. Dies ist ein Beispiel für Pulver aus rostfreiem Stahl 316L, das häufig in μ-MIM-Bauteilen verwendet wird und dessen durchschnittliche Pulvergröße 7 µm beträgt.
Wie die Abbildung zeigt, handelt es sich um Proben mit einem Punktdurchmesser von 15 µm auf der linken Seite und 35 µm auf der rechten Seite, und man kann die Formunterschiede von Zahnrädern und Wellen erkennen. Obwohl es jetzt möglich ist, feinere Formen mit höherer Präzision zu formen, gibt es noch Raum für Verbesserungen. Daher sammeln wir Informationen und Erfahrungen, um Muster präsentieren zu können, die je nach Form der Bauteile unter geeigneten Bedingungen geformt wurden.
Säule
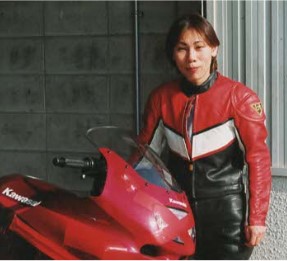
Hallo, ich bin Tomomi Takeno von der Abteilung für allgemeine Angelegenheiten. Ich arbeite seit 11 Monaten für das Unternehmen, und jetzt, wo ich meinen Job gut verstehe, lerne ich täglich neue Zahlen und Sätze, um meine Arbeit effizient zu erledigen. Ich bin darauf bedacht, bei meiner Arbeit angemessen und genau zu kommunizieren, nicht nur, um Unannehmlichkeiten für die Kunden zu vermeiden, sondern auch, weil ich viele Gelegenheiten habe, mit vielen Menschen innerhalb des Unternehmens in Kontakt zu treten.
Fazit
Risse, Absacken oder Blasenbildung werden häufig als Folge des Aufquellens des Bindemittels und/oder der unterschiedlichen Eigenspannungen zwischen der Oberfläche und dem Inneren beobachtet. Diese Probleme lassen sich durch die Auswahl geeigneter organischer Lösungsmittel und durch Temperaturkontrolle vermeiden.
Das katalytische Entbindern nutzt die Sublimation des Bindemittels, wodurch es möglich ist, das Bindemittel in relativ kurzer Zeit zu zersetzen und die Verformung zu minimieren. Bei einer stark sauren Atmosphäre ist die Auswahl an Metallwerkstoffen jedoch begrenzt.
Beim Sinterprozess setzt die Halsbildung („Necking“), d. h. die Ausbildung von Brückenbindungen zwischen Metallpulverkörnern durch thermische Diffusion, bei Erreichen der Sintertemperatur ein. Sobald dieses Necking einsetzt, wird eine Schrumpfung beobachtet, die die Dichte erhöht. Bevor das Necking einsetzt, sollten daher alle organischen Bestandteile zersetzt und das Gas zwischen den Pulverkörnern entfernt werden. Im Sinterprozess führen unerwünschte chemische Reaktionen wie Oxidation oder Karbonisierung zum Verlust mechanischer Eigenschaften, weshalb zu Beginn des Prozesses eine präzise Atmosphärensteuerung mit niedriger Heizrate erforderlich ist. Wenn die Sintertemperatur erreicht ist, können außerdem einige pflanzenbasierte Bindemittel verdampfen.