μ-MIM® Technical Newsletter Vol. 25: Neujahrsgrüße
Vielen Dank, dass Sie unseren technischen Newsletter abonniert haben. Wir möchten Ihnen die besten Wünsche für das neue Jahr von unserem Firmenchef und unseren Mitarbeitern übermitteln.
Präsident
Wir möchten in diesem Jahr eine exponentielle Entwicklung in Bezug auf die Agilität verzeichnen.
Wir haben Verständnis dafür, dass unsere Kunden mit der Lieferzeit für unsere Probemuster nicht zufrieden waren. In der Metall-Spritzgussproduktion ist der Formenbau von entscheidender Bedeutung, da der Spritzgussprozess der einzige Prozess ist, bei dem wir die Morphologie der Komponenten kontrollieren können. Allerdings ist der Formenbau der zeitaufwändigste Prozess in der Metall-Spritzgussproduktion. Wir haben einige technische Entwicklungen wie das hochauflösende 3D-Scannen der Form mit CAD-Datenanalyse oder die Analyse der Spritzgusssimulation eingeführt, um die optimierte Formherstellung zu minimieren. Diese Entwicklungen beschränkten sich jedoch darauf, die Zeit für die Herstellung der Gussform zu verkürzen, und vor allem waren sie nicht in der Lage, die Kosten für die Herstellung der Gussform in der Versuchsphase zu eliminieren. Unsere Versuchsform kann zwar für die Serienproduktion verwendet werden, aber wenn das Design des endgültigen Bauteils in der Versuchsphase nicht bestätigt wird, hat die Investition in die Form einen großen Einfluss auf die Entscheidung unseres Kunden. Daher werden wir in unserer Produktion ein System zur additiven Fertigung von Metallpulvern (Metal AM) installieren.
Wir haben uns in den letzten Jahren mit Metall-AM-Maschinen befasst und schließlich eine Metall-AM-Maschine gefunden, die unseren Anforderungen entspricht und mit unserer Mikro-Metallspritzgusstechnologie (μ-MIM®️) vergleichbar ist. Weitere Informationen zu diesem AM-Fertigungssystem in unserem Unternehmen werden im 1. Quartal 2021 bekannt gegeben. Zur weiteren Verbesserung der Agilität unserer derzeitigen Serienproduktionslinie haben wir digitale Mess- und Steuersysteme installiert. Wir werden einen Schritt nach vorne machen, um ein höheres Niveau der Fertigung und Qualitätskontrolle zu erreichen.
Wir haben unser Metallspritzguss- oder MIM-Herstellungsunternehmen vor 27 Jahren gegründet. Damals war die MIM-Technologie neu und es gab noch viel Raum für Entwicklung. Heute gilt MIM als eine der am weitesten entwickelten Fertigungsmethoden, aber die Popularität ist immer noch geringer als bei anderen Metallverarbeitungsmethoden wie Zerspanung und Stanzen. Der Boom der Metall-AM unterstützt jedoch nicht nur die Anerkennung der Pulvermetallurgie, sondern auch die Entwicklung der umliegenden Technologien und die Kostenreduzierung, z. B. bei der Pulverherstellung, dem Lasersystem, der AM-Maschine usw. Wir werden unsere Fertigungstechnologie weiterentwickeln und diese Vorteile nutzen, um die idealen Komponenten unserer Kunden zu realisieren.
Ich wünsche Ihnen ein frohes neues Jahr und eine gute Entwicklung Ihres Unternehmens. Wir freuen uns auf Ihre Anfragen.
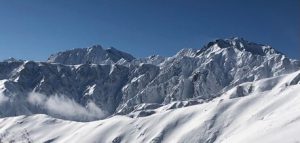
Personal
Wir danken Ihnen, dass Sie uns die Möglichkeit gegeben haben, in den vergangenen Jahren mit Ihnen zusammenzuarbeiten, und wünschen Ihnen allen ein frohes neues Jahr. Im Jahr 2020 gab es nur sehr wenige Gelegenheiten, unsere Kunden persönlich zu treffen. Es war jedoch eine großartige Gelegenheit, die Qualität unserer Webdienste zu verbessern oder unsere internen digitalen Produktionskontrollsysteme zu verbessern. In diesem Jahr werden wir einige Webinare veranstalten, um unsere μ-MIM®️ Technologiefortschritte und Trends in der Pulvermetallurgieindustrie vorzustellen. Wir wünschen uns, dass wir unsere Beziehungen zu Ihnen vertiefen können, und freuen uns darauf, Ihre Ideen für Metallkomponenten zu diskutieren.
Fazit
Risse, Absacken oder Blasenbildung werden häufig als Folge des Aufquellens des Bindemittels und/oder der unterschiedlichen Eigenspannungen zwischen der Oberfläche und dem Inneren beobachtet. Diese Probleme lassen sich durch die Auswahl geeigneter organischer Lösungsmittel und durch Temperaturkontrolle vermeiden.
Das katalytische Entbindern nutzt die Sublimation des Bindemittels, wodurch es möglich ist, das Bindemittel in relativ kurzer Zeit zu zersetzen und die Verformung zu minimieren. Bei einer stark sauren Atmosphäre ist die Auswahl an Metallwerkstoffen jedoch begrenzt.
Beim Sinterprozess setzt die Halsbildung („Necking“), d. h. die Ausbildung von Brückenbindungen zwischen Metallpulverkörnern durch thermische Diffusion, bei Erreichen der Sintertemperatur ein. Sobald dieses Necking einsetzt, wird eine Schrumpfung beobachtet, die die Dichte erhöht. Bevor das Necking einsetzt, sollten daher alle organischen Bestandteile zersetzt und das Gas zwischen den Pulverkörnern entfernt werden. Im Sinterprozess führen unerwünschte chemische Reaktionen wie Oxidation oder Karbonisierung zum Verlust mechanischer Eigenschaften, weshalb zu Beginn des Prozesses eine präzise Atmosphärensteuerung mit niedriger Heizrate erforderlich ist. Wenn die Sintertemperatur erreicht ist, können außerdem einige pflanzenbasierte Bindemittel verdampfen.