μ-MIM® Technical Newsletter Vol. 17: Messtechnik zur Unterstützung der µ-MIM-Technologie
MIM-Teile, die mit unserer µ-MIM-Technologie hergestellt werden, sind klein und komplex geformt, so dass die Messtechnik eine Schlüsseltechnologie ist, die die Qualität von µ-MIM-Produkten unterstützt. In dieser Ausgabe stellen wir die Qualitätssicherungsmessung von kleinen Modulzahnrädern und nicht standardisierten Zahnrädern vor, für die es keine Norm gibt.
Berührende und berührungslose Messmaschinen
Wir setzen berührende und berührungslose 3D-Messmaschinen zur Qualitätskontrolle ein. Die Zahl der Produkte, bei denen die Sonden der berührenden Messmaschine nicht eindringen können, wie z. B. kleine Modulgetriebe und Innenverzahnungen, nimmt ständig zu. Daher nimmt auch die Messrate der berührungslosen Messmaschinen zu. Wir stellen die berührungslosen Messmaschinen vor: eine optische berührungslose 3D-Messmaschine und einen Röntgen-CT-Scanner.
Optischeberührungslose 3D-Messmaschine
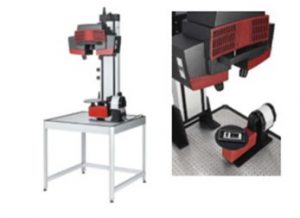
Es ist fast 10 Jahre her, dass das Unternehmen eine optische berührungslose 3D-Messmaschine ATOS triple scan by GOM eingeführt hat. Damals kauften wir es kurz nach seiner Markteinführung in der Annahme, dass es die höchste Auflösung aller optischen Messmaschinen erreichen könnte. Dies ist eine Art von Dimensionsmessmaschine, die auch heute noch sehr kleine Objekte mit der höchsten Auflösung messen kann.
Röntgen-CT-Messgerät

Für die Auswertung wird der CT-Scanner MCT225 von Nikon verwendet. Im Gegensatz zu einem optischen Messgerät gibt es keinen Einfluss durch Oberflächenreflexion. Daher ist eine Vorbehandlung wie eine Oberflächenbeschichtung nicht erforderlich. Darüber hinaus kann er zur Messung von Innenverzahnungen verwendet werden, da es möglich ist, aus den Eigenschaften der Röntgenstrahlen zerstörungsfreie numerische Daten über die innere Struktur zu erhalten.
Messung in µ-MIM-Technologie
Eine hochauflösende Messmaschine ist für die Bewertung der Qualität unserer Mikro-Metallspritzgussteile (µ-MIM) erforderlich. Allerdings sind die Technologien, die Erfahrungen zur Analyse der Daten und die Vorverarbeitung der Proben unverzichtbar.
Zusätzlich zu diesen Technologien und Erfahrungen haben wir eine Analysetechnik für die Zahnoberflächen entwickelt. Sie vergleicht die Analysedaten aus dem Röntgen-CT-Scanner und der optischen Messung mit 3D-Modelldaten. Wir bieten unseren Kunden unsere Mikro-Metall-Spritzguss-Produkte (µ-MIM) mit den Ergebnissen dieser einzigartig entwickelten Analysetechnologie an. Wir führen auch Analysen von Teilen durch, die nicht unsere Produkte sind.
Säule
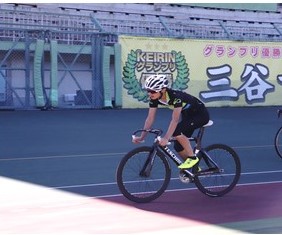
Hallo. Ich bin Tomori Shimada, der für den Sinterprozess zuständig ist. Ich bin seit über 1 Jahr im Unternehmen. Mein Motto ist es, immer zu lächeln, und ich lächle viel bei der Arbeit. Ich werde mein Wissen über den Sinterofen, mit dem ich täglich in Kontakt komme, nach und nach vertiefen. Meine Hobbys sind Radfahren. Letzte Woche hatte ich die Gelegenheit, an einem Radrennen auf einer Bahnbank teilzunehmen. Beim Radrennen fahre ich immer ein 1-km-Zeitfahren, aber ich konnte die Zeit um 2 Sekunden auf 1 Minute und 26 Sekunden verkürzen.
Fazit
Risse, Absacken oder Blasenbildung werden häufig als Folge des Aufquellens des Bindemittels und/oder der unterschiedlichen Eigenspannungen zwischen der Oberfläche und dem Inneren beobachtet. Diese Probleme lassen sich durch die Auswahl geeigneter organischer Lösungsmittel und durch Temperaturkontrolle vermeiden.
Das katalytische Entbindern nutzt die Sublimation des Bindemittels, wodurch es möglich ist, das Bindemittel in relativ kurzer Zeit zu zersetzen und die Verformung zu minimieren. Bei einer stark sauren Atmosphäre ist die Auswahl an Metallwerkstoffen jedoch begrenzt.
Beim Sinterprozess setzt die Halsbildung („Necking“), d. h. die Ausbildung von Brückenbindungen zwischen Metallpulverkörnern durch thermische Diffusion, bei Erreichen der Sintertemperatur ein. Sobald dieses Necking einsetzt, wird eine Schrumpfung beobachtet, die die Dichte erhöht. Bevor das Necking einsetzt, sollten daher alle organischen Bestandteile zersetzt und das Gas zwischen den Pulverkörnern entfernt werden. Im Sinterprozess führen unerwünschte chemische Reaktionen wie Oxidation oder Karbonisierung zum Verlust mechanischer Eigenschaften, weshalb zu Beginn des Prozesses eine präzise Atmosphärensteuerung mit niedriger Heizrate erforderlich ist. Wenn die Sintertemperatur erreicht ist, können außerdem einige pflanzenbasierte Bindemittel verdampfen.