μ-MIM® Technical Newsletter Vol. 19: Entwicklung der additiven Fertigung Vol. 1 (Metal AM outline)
Die Technologie der additiven Fertigung (AM) wurde in Japan aktiv entwickelt, seit AM 2016 als nationales Projekt gefördert wurde. Wir möchten die AM-Trends aus der Perspektive der Hersteller von Metall-Spritzgussteilen oder MIM vorstellen.
Klassifizierung nach Pulverzufuhr und Druckverfahren
Bei der Zufuhr von Metallpulver, das im Metall-3D-Drucker verwendet wird, gibt es grob 2 Methoden. Die eine ist die Zuführung zum Druckteil vor Ort durch eine Düse und die andere ist die Verteilung des Pulvers über die vorhandene Schicht durch eine Rolle im Voraus. Die Vor-Ort-Zuführung über eine Düse hat eine höhere Materialausbeute als die Stapelung über eine Rolle, da das zugeführte Pulver zu fast 100 % verbraucht wird. Allerdings müssen ausreichend viele Säulen gebildet werden, um die Produktstruktur während des Prozesses zu stützen, so dass die Gesamtmaterialausbeute in vielen Fällen gering ist. Bei der Stapelung von Schichten mit Hilfe von Walzen muss das Pulver gleichmäßig auf der gesamten Verarbeitungsfläche verteilt werden, so dass die Materialausbeute gering ist. Allerdings dient das unverbrauchte Pulver während des Prozesses als Stützsäule, so dass sich die Nachbearbeitungsschritte nach dem Druck reduzieren lassen. Außerdem wird heutzutage ein hoher Prozentsatz des nicht verwendeten Pulvers wiederverwendet. Das Druckverfahren kann in selektives Sintern (SS) und Binder-Jetting unterschieden werden. Während beim selektiven Sintern das Metallpulver während des Drucks gesintert wird, ist beim Binder Jetting nach dem Druck ein Entbindern und Sintern wie beim Metallspritzguss oder MIM erforderlich. Beim Binder Jetting wird der Klebstoff auf eine gewünschte Fläche gedruckt, um das Metallpulver zu einer Produktstruktur zu verbinden. Die Wärmequelle in SS wurde intensiv untersucht und die Druckgeschwindigkeit in den letzten Jahren drastisch erhöht. Im Jahr 2016 wurde eine Druckmaschine mit 50 cm³/Stunde auf den Markt gebracht, und es wird angestrebt, mit der nächsten Maschinengeneration 250 cm³/Stunde oder sogar 1000 cm³/Stunde zu erreichen. Die Druckgeschwindigkeit des Bindemittelstrahls ist höher als bei der SS. Eine Maschine mit einer Druckgeschwindigkeit von 60-100 cm³/Stunde ist bereits auf dem Markt.
Metallpulver für die Metall-AM
Bei der Metall-AM wird das kugelförmige Pulver ebenso verwendet wie beim Metallspritzguss oder MIM. Beim Metall-Spritzguss oder der MIM-Herstellung gibt es nur wenige Probleme, wenn die feinen Metallpulver gemischt werden. Bei der Metall-AM hingegen führen zu kleine Partikel zu einer Verschlechterung der Druckqualität. Daher werden bei der Metall-AM in der Regel sowohl eine obere als auch eine untere Größengrenze festgelegt. Da außerdem die Reduktionsreaktion während des SS-Sinterprozesses nicht zu erwarten ist, wird das durch teure Gaszerstäubung hergestellte Metallpulver am häufigsten verwendet. Aufgrund dieser Einschränkungen ist das AM-Pulver sogar teurer als Metallspritzguss- oder MIM-Pulver, das in der herkömmlichen Pulvermetallurgie am teuersten ist.
Hürdevon "30µm"
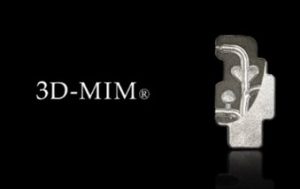
Ein 3D-Metalldrucker enthält eine Reihe neuester Technologien, wie die Verwendung von Pulver mit streng begrenzter Partikelgröße, mehrere Wärmequellen und ein hochpräzises System zur Steuerung beweglicher Teile. Die Entwicklung von 3D-Metalldruckern in den letzten Jahren ist bemerkenswert und hat sicher auch anderen Branchen große Vorteile gebracht. Allerdings scheint es noch immer eine hohe Hürde für die Kontrolle von Abmessungen von ≤ 30 µm zu geben. Der 3D-Drucker hat an Produktivität gewonnen, um mit anderen Metallverarbeitungsmethoden konkurrieren zu können, aber es ist notwendig, auf einen weiteren Durchbruch zu warten, um die Toleranzanforderungen von ≤ 30 µm zu erfüllen. Unser Fertigungsbereich, Taisei Kogyo Co., Ltd. verfügt über µ-MIM® (Micro MIM) und 3D-MIM®, mit denen komplexe Formen mit einer Genauigkeit von ± 10 µm bei einer Teilegröße von ≤ 5 mm in Serie gefertigt werden können. Wir tragen kontinuierlich zur Entwicklung der 3D-Druckertechnologie aus Metall bei, indem wir unser Know-how im Bereich des Entbinderns und Sinterns durch Metall-Spritzgießen oder MIM-Fertigung weiterentwickeln.
Säule
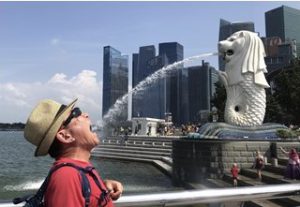
Ich bin Hikoji Okuyama, zuständig für Forschung und Entwicklung in Japan. Ich bin erst seit März 2019 im Unternehmen, also relativ neu. Obwohl ich nicht mehr jung bin, entdecke ich jeden Tag etwas Neues in der Welt der Metalle, was ein tiefes Wissen erfordert. Ich glaube, das hält mein Gehirn scharf! An den Wochenenden spiele ich Tennis und fahre Rad. Im Winter fahre ich auch gerne Ski. Eine andere Sache, die mir Spaß macht, ist das Reisen - letztes Jahr war ich mit meinem Sohn im Winter in den skandinavischen und baltischen Ländern. Das war wirklich kalt!
Fazit
Risse, Absacken oder Blasenbildung werden häufig als Folge des Aufquellens des Bindemittels und/oder der unterschiedlichen Eigenspannungen zwischen der Oberfläche und dem Inneren beobachtet. Diese Probleme lassen sich durch die Auswahl geeigneter organischer Lösungsmittel und durch Temperaturkontrolle vermeiden.
Das katalytische Entbindern nutzt die Sublimation des Bindemittels, wodurch es möglich ist, das Bindemittel in relativ kurzer Zeit zu zersetzen und die Verformung zu minimieren. Bei einer stark sauren Atmosphäre ist die Auswahl an Metallwerkstoffen jedoch begrenzt.
Beim Sinterprozess setzt die Halsbildung („Necking“), d. h. die Ausbildung von Brückenbindungen zwischen Metallpulverkörnern durch thermische Diffusion, bei Erreichen der Sintertemperatur ein. Sobald dieses Necking einsetzt, wird eine Schrumpfung beobachtet, die die Dichte erhöht. Bevor das Necking einsetzt, sollten daher alle organischen Bestandteile zersetzt und das Gas zwischen den Pulverkörnern entfernt werden. Im Sinterprozess führen unerwünschte chemische Reaktionen wie Oxidation oder Karbonisierung zum Verlust mechanischer Eigenschaften, weshalb zu Beginn des Prozesses eine präzise Atmosphärensteuerung mit niedriger Heizrate erforderlich ist. Wenn die Sintertemperatur erreicht ist, können außerdem einige pflanzenbasierte Bindemittel verdampfen.