Diameter less than 1 mm, module of < 0.3 mm!
Da viele Arten von Präzisionsgeräten immer kleiner und leichter werden, müssen auch die Zahnräder in den Geräten kleiner und leichter werden. Es ist schwierig, kleine, speziell geformte Zahnräder wie Kegel- und Schrägstirnräder mit Durchmessern von weniger als ein paar Millimetern zu bearbeiten. Unsere Konzerngesellschaft Taisei Kogyo Co. Ltd. hat jedoch die Forschung und Entwicklung von speziell geformten Mikrozahnrädern, die mit der μ-MIM®-Technologie hergestellt werden, fortgesetzt. MIM (Metallpulverspritzguss) wird üblicherweise für die Serienproduktion von Zahnrädern eingesetzt, aber unsere μ-MIM®-Technologie stellt spezielle kleine Zahnräder mit stabiler Qualität her.
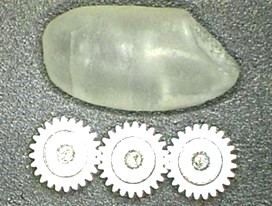
Hochpräzise Verarbeitung durch μ-MIM®
- Maßgenauigkeit ±0,1% wird erreicht
Das MIM-Verfahren beginnt mit dem Mischen von Metallpulver und Bindemittelharzen, um das Ausgangsmaterial zusammenzustellen. Das Ausgangsmaterial wird in die Form gespritzt, um das Bauteil zu formen, und anschließend entbindert und gesintert, um das Metallteil zu erhalten. Im Gegensatz zum Kunststoffspritzguss ist beim MIM-Verfahren ein Entbinderungs- und Sinterungsschritt erforderlich, bei dem die Bauteile um mehr als 10 % schrumpfen. Daher führen die meisten MIM-Hersteller eine sekundäre Verarbeitung wie z. B. eine maschinelle Bearbeitung durch, um die Nettoform zu erreichen. Unsere μ-MIM®-Technologie geht jedoch über das herkömmliche MIM-Verfahren hinaus und ist in der Lage, netzförmige Bauteile im gesinterten Zustand herzustellen.
Nachfolgend finden Sie einige Beispiele für Zahnräder, die wir hergestellt haben. Wenn Sie Interesse haben, können Sie sich hier über den Unterschied zwischen herkömmlichem MIM und μ-MIM® informieren.
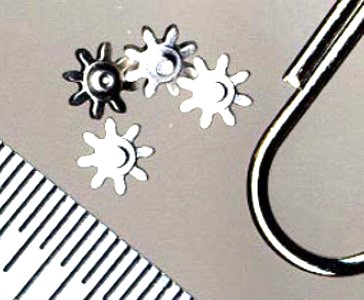
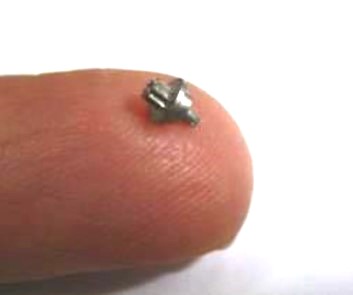
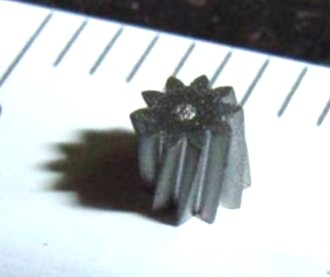
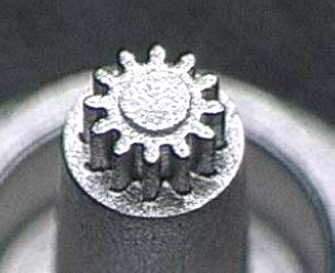
Spanende Bearbeitung vs. μ-MIM®
Nahezu alle Arten von Formen lassen sich mit Hilfe von 5-Achsen-Werkzeugmaschinen und computergestützter Fertigungssoftware realisieren, doch je komplexer die Form ist, desto schwieriger wird es, eine hohe Präzision zu erreichen, was die Bearbeitungszeit und die Kosten erhöht. So sind z. B. spiralförmige Kegelräder, schrägverzahnte Zahnräder und innenverzahnte Zahnräder typische Zahnräder, deren Herstellung durch Fräsen sehr schwierig und teuer ist.
Diese Teile erfordern eine lange Bearbeitungszeit, wenn sie durch Schneiden oder Zerspanen hergestellt werden, so dass die Serienproduktion in großen Mengen begrenzt ist. Um die Herstellungskosten niedrig zu halten, werden in einigen Fällen die Designkomponenten so modifiziert, dass sie mit einer Drehbank, einer Fräsmaschine oder einem NC (allgemeines 3-Achsen-Bearbeitungszentrum) bearbeitet werden können.
Unser μ-MIM® ermöglicht jedoch eine stabile Massenproduktion solcher Komponenten, sogar dieses schrägverzahnte Zahnrad, das unmöglich aus einer Standardformstruktur entformt werden kann. Außerdem müssen wir im Gegensatz zur maschinellen Bearbeitung die Spannvorrichtung nicht neu einstellen, und auch die geforderten Lagetoleranzen werden in hohem Maße eingehalten. Außerdem setzt unser 3D-μMIM, ein Teil unserer μ-MIM®-Technologie, der Gestaltungsfreiheit keine Grenzen, so dass jedes ideale Zahnrad mit μ-MIM® stabil in Serie gefertigt werden kann.
In der nächsten Ausgabe unseres Newsletters werden wir erklären, wie dieses Problem gelöst werden kann und welche Vorteile die Herstellung von Zahnrädern mit μ-MIM® bietet.
Der Frühling ist da!
In Japan sind viele Menschen von einer bestimmten Blumenart besessen - Sakura (Kirschblüte)! Wahrscheinlich haben Sie in den Medien gesehen, dass viele Japaner ein Picknick unter den Kirschblütenbäumen machen. Die Kirschblüten blühen zwischen Ende März und Ende April, je nachdem, wo in Japan Sie sich befinden. Da einige Arbeitnehmer in dieser Zeit ihre Abteilung wechseln oder Neulinge anfangen zu arbeiten, weil das japanische Schul- und Geschäftsjahr im April beginnt und im März endet, werden Willkommens- oder Abschiedsfeiern von Unternehmen oft unter Kirschblütenbäumen abgehalten. Wenn Sie bereit sind, nach Japan zu reisen, empfehlen wir Ihnen diese schöne Jahreszeit für einen Besuch in Japan!
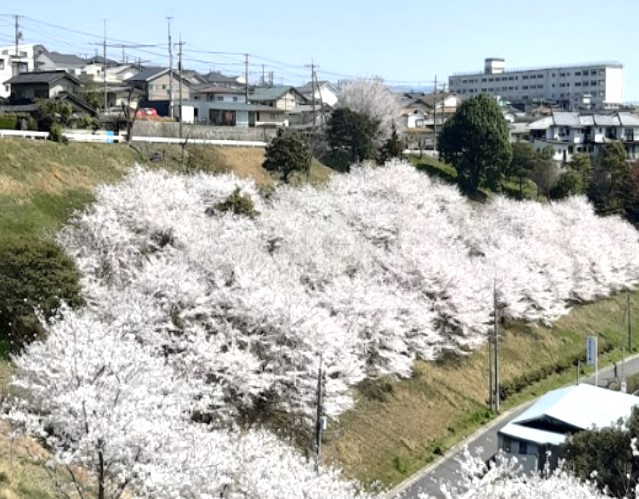
Download der PDF-Datei
Fazit
Risse, Absacken oder Blasenbildung werden häufig als Folge des Aufquellens des Bindemittels und/oder der unterschiedlichen Eigenspannungen zwischen der Oberfläche und dem Inneren beobachtet. Diese Probleme lassen sich durch die Auswahl geeigneter organischer Lösungsmittel und durch Temperaturkontrolle vermeiden.
Das katalytische Entbindern nutzt die Sublimation des Bindemittels, wodurch es möglich ist, das Bindemittel in relativ kurzer Zeit zu zersetzen und die Verformung zu minimieren. Bei einer stark sauren Atmosphäre ist die Auswahl an Metallwerkstoffen jedoch begrenzt.
Beim Sinterprozess setzt die Halsbildung („Necking“), d. h. die Ausbildung von Brückenbindungen zwischen Metallpulverkörnern durch thermische Diffusion, bei Erreichen der Sintertemperatur ein. Sobald dieses Necking einsetzt, wird eine Schrumpfung beobachtet, die die Dichte erhöht. Bevor das Necking einsetzt, sollten daher alle organischen Bestandteile zersetzt und das Gas zwischen den Pulverkörnern entfernt werden. Im Sinterprozess führen unerwünschte chemische Reaktionen wie Oxidation oder Karbonisierung zum Verlust mechanischer Eigenschaften, weshalb zu Beginn des Prozesses eine präzise Atmosphärensteuerung mit niedriger Heizrate erforderlich ist. Wenn die Sintertemperatur erreicht ist, können außerdem einige pflanzenbasierte Bindemittel verdampfen.