Vergleiche und Merkmale von Verdichtung, MIM und HIP in Bezug auf die Dichte
Pulvermetallurgisch hergestellte Metallteile haben in der Regel eine geringere Dichte als maschinell bearbeitete oder gestanzte Knetwerkstoffe. Obwohl eine niedrige Dichte je nach Anwendung von Vorteil sein kann, ist im Allgemeinen eine hohe Dichte erforderlich, um die in der Entwurfsphase angenommenen Anforderungen an die mechanische Festigkeit zu erfüllen. In dieser Ausgabe stellen wir die Merkmale der Pulvermetallurgie unter dem Gesichtspunkt der Dichte vor.
Vergleich zwischen pulvermetallurgischen Verfahren
Die Dichte von gesinterten Bauteilen, die durch Metallspritzguss (MIM) oder Pulverpressen (CM) hergestellt werden, weist im Verhältnis zur theoretischen Dichte einen geringen Prozentsatz an Hohlräumen auf. Bei der Verwendung von Edelstahlpulver werden Sinterteile mit einer Dichte von etwa 92 % im Pressverfahren und über 98 % im MIM-Verfahren hergestellt. Wird eine Dichte von über 98 % erreicht, haben Hohlräume keinen großen Einfluss auf die Zugfestigkeit. Wenn jedoch selbst einige Prozent Hohlräume nicht zulässig sind, wird das heißisostatische Pressen (HIP) als Nachbearbeitung eingesetzt.
Merkmale von Verdichtung, MIM und HIP
CM ist das produktivste Verfahren in der Pulvermetallurgie. Da das Pulver mit nur wenigen Volumenprozent des Bindemittels verdichtet wird, ist der Entbinderungsprozess kürzer als beim MIM. Beim CM wird das Pulver komprimiert und verformt, wodurch die Oxidschicht auf der Oberfläche des Metallpulvers zerstört wird. Das Ergebnis ist, dass die frischen Metalloberflächen in Kontakt kommen, weshalb eine relativ kurze Sinterzeit erforderlich ist. Obwohl es viele Einschränkungen bei der CM-Konstruktion gibt, ist es möglich, die Maßgenauigkeit auf hohem Niveau zu kontrollieren. Mit dem Verfahren können Sinterteile mit einer Genauigkeit von ± 0,004 mm/mm in der Druckrichtung und ± 0,002 mm/mm in der Querrichtung des Drucks hergestellt werden. Da bei der Verdichtung jedoch Metallpulver mit größeren Partikeln als beim MIM-Verfahren verwendet wird und die Bauteile aufgrund der Verteilung der Kompressibilität des Pulvers in den verdichteten Teilen nicht bei hohen Temperaturen gesintert werden können, ist die Dichte der gesinterten Edelstahlbauteile mit etwa 92 % relativ gering, was sich auf den Formabstand und die Produktivität auswirkt.
MIM ist ein Verfahren mit moderater Maßtoleranz und Produktivität, und im Vergleich zu CM hat MIM einen hohen Grad an Gestaltungsfreiheit und eine höhere Dichte. Das Bindemittel wird mit Metallpulver in einem Verhältnis von etwa 40 Volumenprozent gemischt, um Bauteile zu formen. Daher hat MIM Vorteile bei der Herstellung komplizierter Formen und der Massenproduktion relativ kleiner Bauteile. Im Gegensatz zur Verdichtung wird das Metallpulver während des Formprozesses nicht verformt, und die Verteilung des Metallpulvers im Bauteil ist gleichmäßig, so dass eine Verformung selbst beim Sintern bei relativ hoher Temperatur unterdrückt werden kann, wodurch Sinterteile mit hoher Dichte entstehen. Da beim MIM-Verfahren Pulver mit geringer Partikelgröße verwendet wird, wird ein Ausgangsmaterial mit superfeinem Pulver entwickelt, das eine hohe Übertragbarkeit aufweist. Es ist auch möglich, das restliche Pulver aus dem AM (Additive Manufacturing) zu verwenden, das außerhalb der Spezifikation lag. Im Allgemeinen wird HIP häufig verwendet, um die Dichte von Sinterkörpern zu erhöhen, die durch CM, MIM oder Gussteile hergestellt werden, aber es wird auch für die Herstellung großer Metallteile aus dem Pulver verwendet. Die HIP-Pulverherstellung wird nur für Teile verwendet, die in rauen Umgebungen betrieben werden, wie z. B. kleine Mengen von Rohrverbindungsteilen für Offshore-Ölbohrungen oder sehr begrenzte Stückzahlen, da die Form nur einmal verwendet wird. Beim Sintern mit HIP kann ein Teil mit hoher Dichte hergestellt werden. Da jedoch hochreines Pulver in einen versiegelten Einwegbehälter gefüllt und gesintert wird, ist die Produktivität gering, und es ist schwierig, kleine Teile herzustellen.
Merkmale der Mikro-MIM-Technologie
Die Micro MIM-Gruppe hat die originale μ-MIM-Technologie® auf der Grundlage der herkömmlichen MIM-Technologie entwickelt und ist auf kleine und komplex geformte Bauteile spezialisiert. Mit rostfreiem Stahl können wir eine Dichte von mehr als 98,5% und eine Toleranz von ±0,010 mm für Komponenten kleiner als 5 mm erreichen. Wir haben eine Methode zur Minimierung von Sekundärprozessen wie Bearbeitung und Formenbau entwickelt, die es uns ermöglicht, Nettoformen mit stabiler, hoher Qualität herzustellen. Gerne zeigen wir Ihnen unsere μ-MIM-Bauteile mit der Lupe, wenn wir Sie persönlich treffen.
Grüße aus Düsseldorf, Deutschland
Hallo, ich bin Yumi Peinemann, Marketing und Account Manager. Ich bin schon seit kurz vor der Gründung des Unternehmens dabei. Da die Unternehmenskultur mich ermutigt, neue Herausforderungen anzunehmen, versuche ich jeden Tag, neue Ideen zu entwickeln und an neuen Dingen zu arbeiten.
In Deutschland sind Brettspiele über alle Generationen hinweg sehr beliebt, und dieses Umfeld hat mich dazu gebracht, ein Brettspieler zu werden. Ich sammle Brettspiele auf meinen Reisen und spiele sie gerne in Parks und zu Hause. Wenn Sie einmal in Deutschland sind, kommen Sie vorbei und lassen Sie uns gemeinsam deutsche Brettspiele spielen!
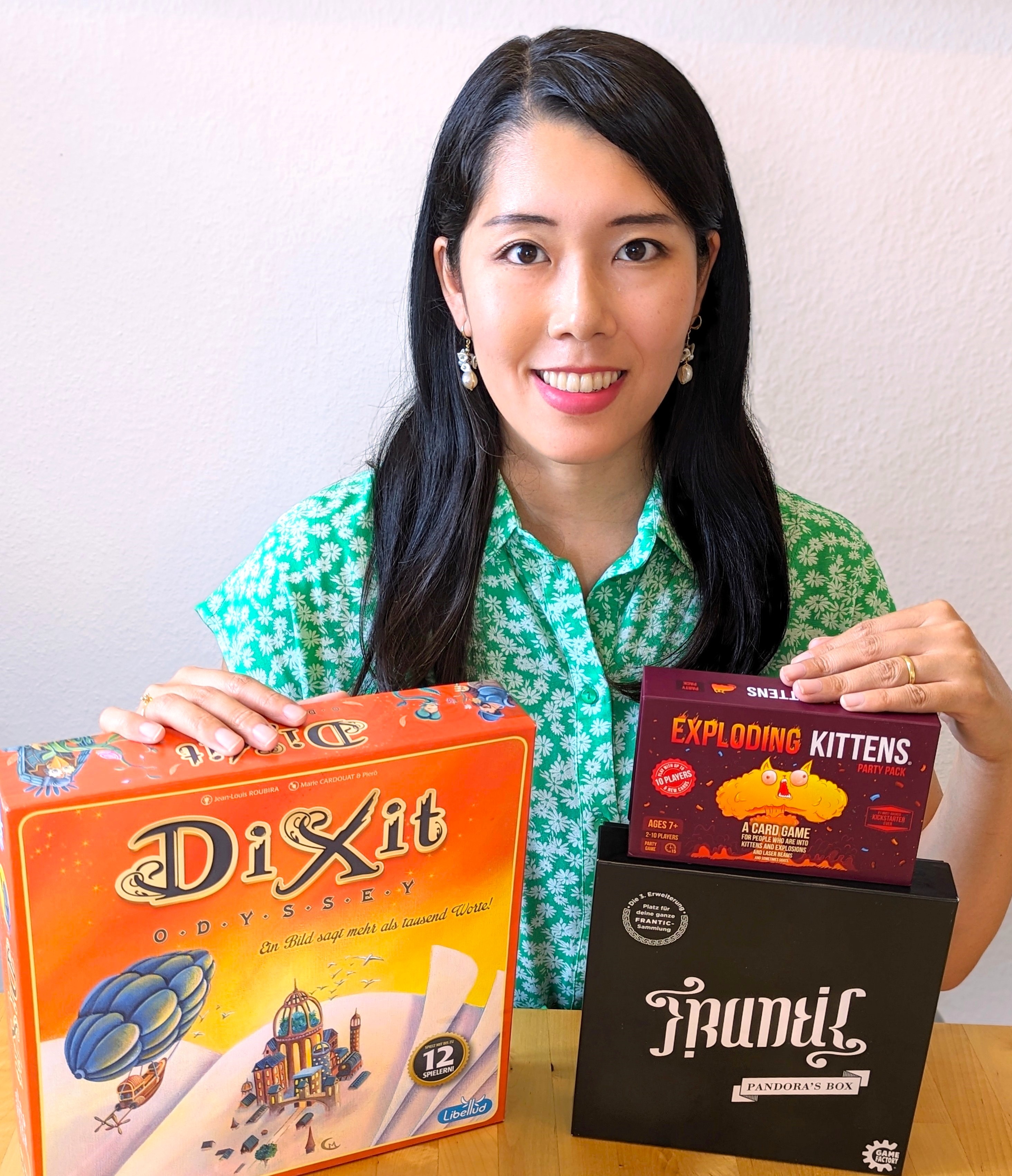
Download der PDF-Datei
Fazit
Risse, Absacken oder Blasenbildung werden häufig als Folge des Aufquellens des Bindemittels und/oder der unterschiedlichen Eigenspannungen zwischen der Oberfläche und dem Inneren beobachtet. Diese Probleme lassen sich durch die Auswahl geeigneter organischer Lösungsmittel und durch Temperaturkontrolle vermeiden.
Das katalytische Entbindern nutzt die Sublimation des Bindemittels, wodurch es möglich ist, das Bindemittel in relativ kurzer Zeit zu zersetzen und die Verformung zu minimieren. Bei einer stark sauren Atmosphäre ist die Auswahl an Metallwerkstoffen jedoch begrenzt.
Beim Sinterprozess setzt die Halsbildung („Necking“), d. h. die Ausbildung von Brückenbindungen zwischen Metallpulverkörnern durch thermische Diffusion, bei Erreichen der Sintertemperatur ein. Sobald dieses Necking einsetzt, wird eine Schrumpfung beobachtet, die die Dichte erhöht. Bevor das Necking einsetzt, sollten daher alle organischen Bestandteile zersetzt und das Gas zwischen den Pulverkörnern entfernt werden. Im Sinterprozess führen unerwünschte chemische Reaktionen wie Oxidation oder Karbonisierung zum Verlust mechanischer Eigenschaften, weshalb zu Beginn des Prozesses eine präzise Atmosphärensteuerung mit niedriger Heizrate erforderlich ist. Wenn die Sintertemperatur erreicht ist, können außerdem einige pflanzenbasierte Bindemittel verdampfen.