μ-MIM® Technical Newsletter Vol. 20: Fertigung Teil 2 - Zusammenarbeit von Metall-AM und Metall-Spritzgießen (MIM)
Heute stellen wir Ihnen unseren Ansatz für die Zusammenarbeit mit AM und unseren Interessenten vor.
Zusammenfassung von Metall AM
Heutzutage sind verschiedene Metall-AM-Geräte entwickelt worden, die in einem harten Wettbewerb um das Überleben auf dem Markt stehen. Es gibt Stärken und Schwächen, die sich aus ihren Herstellungsverfahren ergeben, die in der folgenden Tabelle zusammengefasst sind.
Die Tabelle klassifiziert repräsentative AM-Methoden nach der Verdichtungsphase.
Vergleichstabelle repräsentativer Metall-AM-Methoden
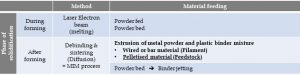
Koexistenz von MIM und AM
Der Prozess, der Verdichtungsschritt kommt nach dem Formen, erfordert Entbinderungs- und Sinterungsschritte, die gleich und wesentlich sind wie beim Metall-Spritzguss oder MIM-Prozess. Daher können wir unsere Metallspritzguss-Verarbeitungstechnologie auf einige Metall-AM-Verfahren anwenden. Bei der FDM-Methode (Fused Deposition Modeling), die in der Tabelle fett gedruckt ist, wird in der Regel ein Draht oder ein stabförmiges Filament verwendet, um den Grünkörper zu formen. Kürzlich wurde ein Metall-AM-Gerät* auf den Markt gebracht, das direkt mit pelletiertem MIM-Rohmaterial arbeitet. Daher kann man sagen, dass die FDM-Methode der beste Weg für MIM-Hersteller ist, mit der AM-Fertigung zusammenzuarbeiten. Da wir über Kenntnisse und Erfahrungen mit unserem Ausgangsmaterial aus unserer Geschichte der Metall-Spritzgussproduktion verfügen, sollten unsere Techniken des Entbinderns und Sinterns sowie des Formens auch bei Metall-AM-Geräten effektiv sein. Wir glauben, dass diese Zusammenarbeit zu einem besseren Service für unsere Kunden führen wird, insbesondere in der Phase der Prototypenherstellung.
Unser Ansatz für die AM-Herstellung
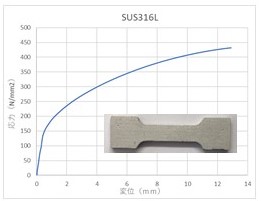
Wir haben Studien mit unserem ursprünglichen Ausgangsmaterial durchgeführt, das in einem FDM-Metall-AM-Gerät verwendet wurde, und die mechanischen Eigenschaften beobachtet. Das rechts abgebildete Diagramm ist das Ergebnis eines Zugtests. Wir sind zuversichtlich, dass wir denjenigen, die Probleme mit der Metall-AM-Herstellung haben, unser Ausgangsmaterial für AM-Versuche anbieten können. Bitte zögern Sie nicht, uns zu kontaktieren.
Säule
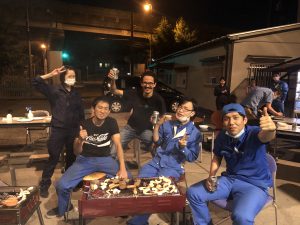
In der Zentrale von Micro MIM Japan Holdings Inc. und Taisei Kogyo Co. in Osaka, Japan, veranstalten wir zweimal im Jahr einen Grillabend. Dieser wird von einigen der jungen Kollegen, die in der Zentrale arbeiten, organisiert. Die Veranstaltung beginnt um 18.00 Uhr, wenn alle mit der Arbeit fertig sind. Beim letzten Mal haben wir einen PC mitgebracht und uns mit den Kollegen in Thailand und Deutschland verbunden. Das war eine gute Gelegenheit für alle, sich gegenseitig zu begrüßen und zu sehen, wie es den Kollegen an anderen Standorten geht. Besonders nach dem Lockdown waren die Leute froh, sich auch online zu sehen. Der Nachteil für diejenigen, die nicht in Japan sind, war, dass wir arbeiten mussten, während sich die Kollegen in Japan mit Bier und BBQ vergnügten!
Fazit
Risse, Absacken oder Blasenbildung werden häufig als Folge des Aufquellens des Bindemittels und/oder der unterschiedlichen Eigenspannungen zwischen der Oberfläche und dem Inneren beobachtet. Diese Probleme lassen sich durch die Auswahl geeigneter organischer Lösungsmittel und durch Temperaturkontrolle vermeiden.
Das katalytische Entbindern nutzt die Sublimation des Bindemittels, wodurch es möglich ist, das Bindemittel in relativ kurzer Zeit zu zersetzen und die Verformung zu minimieren. Bei einer stark sauren Atmosphäre ist die Auswahl an Metallwerkstoffen jedoch begrenzt.
Beim Sinterprozess setzt die Halsbildung („Necking“), d. h. die Ausbildung von Brückenbindungen zwischen Metallpulverkörnern durch thermische Diffusion, bei Erreichen der Sintertemperatur ein. Sobald dieses Necking einsetzt, wird eine Schrumpfung beobachtet, die die Dichte erhöht. Bevor das Necking einsetzt, sollten daher alle organischen Bestandteile zersetzt und das Gas zwischen den Pulverkörnern entfernt werden. Im Sinterprozess führen unerwünschte chemische Reaktionen wie Oxidation oder Karbonisierung zum Verlust mechanischer Eigenschaften, weshalb zu Beginn des Prozesses eine präzise Atmosphärensteuerung mit niedriger Heizrate erforderlich ist. Wenn die Sintertemperatur erreicht ist, können außerdem einige pflanzenbasierte Bindemittel verdampfen.